設備トラブルから解放!IATF 16949のTPM成功のポイント
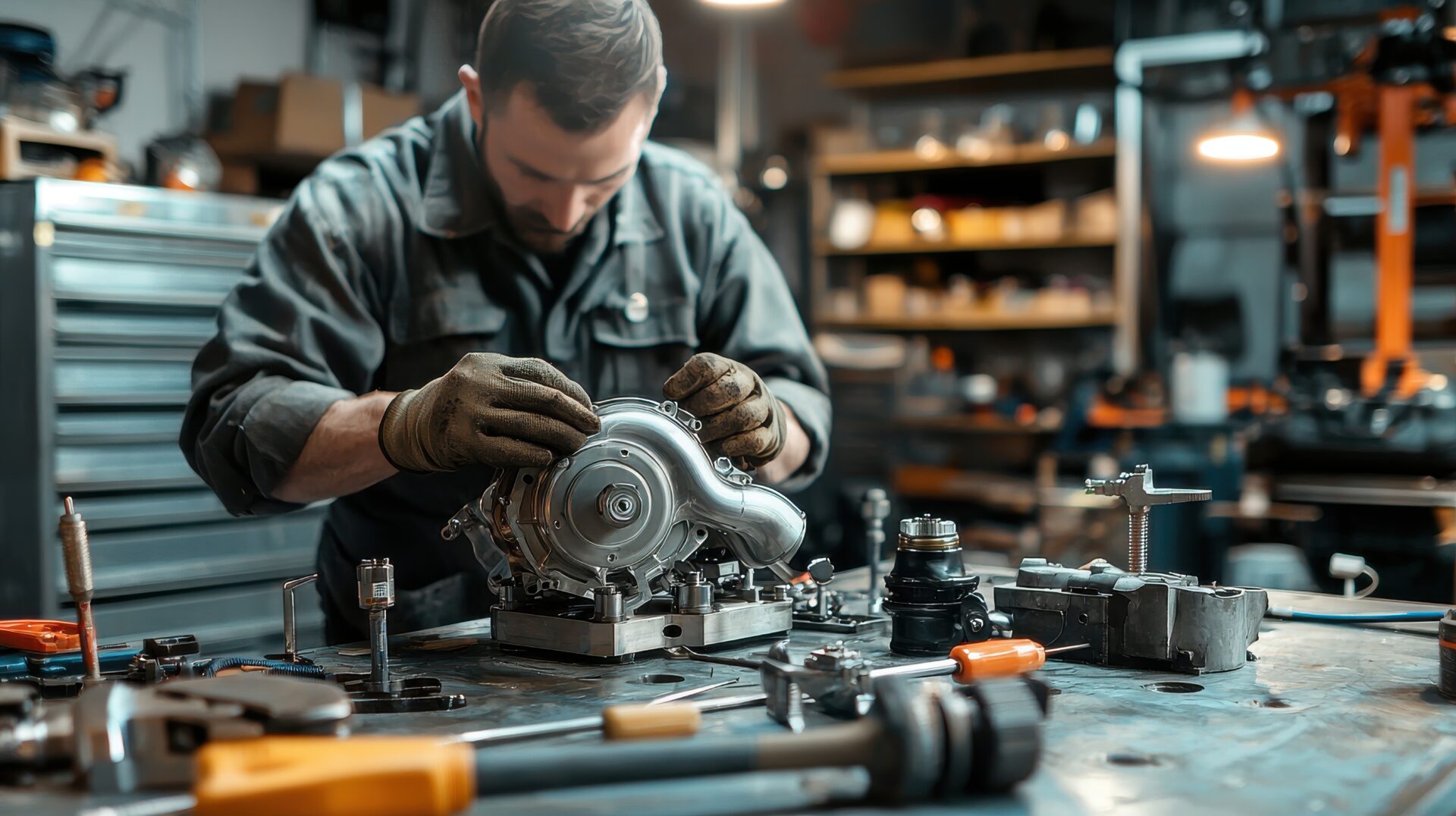
はじめに
この記事は、IATF 16949で要求されている設備の管理において、以下の関心をお持ちの方に向けて作られています。
- 予防保全に取り組んでいるつもりなのに、設備故障がなかなか減らず困っている…
- 設備トラブルでラインが止まり、納期に影響を与えてしまうことがあって焦る…
- ベテラン保全担当者の技術伝承がうまく進まず、ノウハウが属人化してしまっている…
- 不良発生率・クレーム件数をなかなか下げられず、品質目標を達成できない…
あなたもこうしたお悩みや課題はありませんか?もし、こうした悩みを抱えていらっしゃるとしたら、それは決して珍しいことではありません。
自動車部品などの製造業では、設備の安定稼働と品質不良ゼロの実現が常に大きなテーマですが、認証取得のみをゴールにしてしまうと、その後に想定以上のコストやリスクが発生してしまうケースが多々あります。特に、IATF 16949はISO9001と比較して要求事項が格段に多く、現場レベルまで正しい理解や運用が浸透しなければ、せっかくの認証が形骸化してしまう恐れもあります。
当社は「認証を競争優位のコアに据えて、企業価値を継続的に高める」ことを目的としたコンサルティングやトレーニング、内部監査支援を提供しています。本記事では、TPMを通じて現場の保全活動をレベルアップし、不良・故障ゼロを目指す保全(特にTPM)とIATF 16949の要求事項を両立させるポイントを中心に、現役のIATF 16949/JIS Q 9100審査員資格を有する当社代表がわかりやすく解説します。
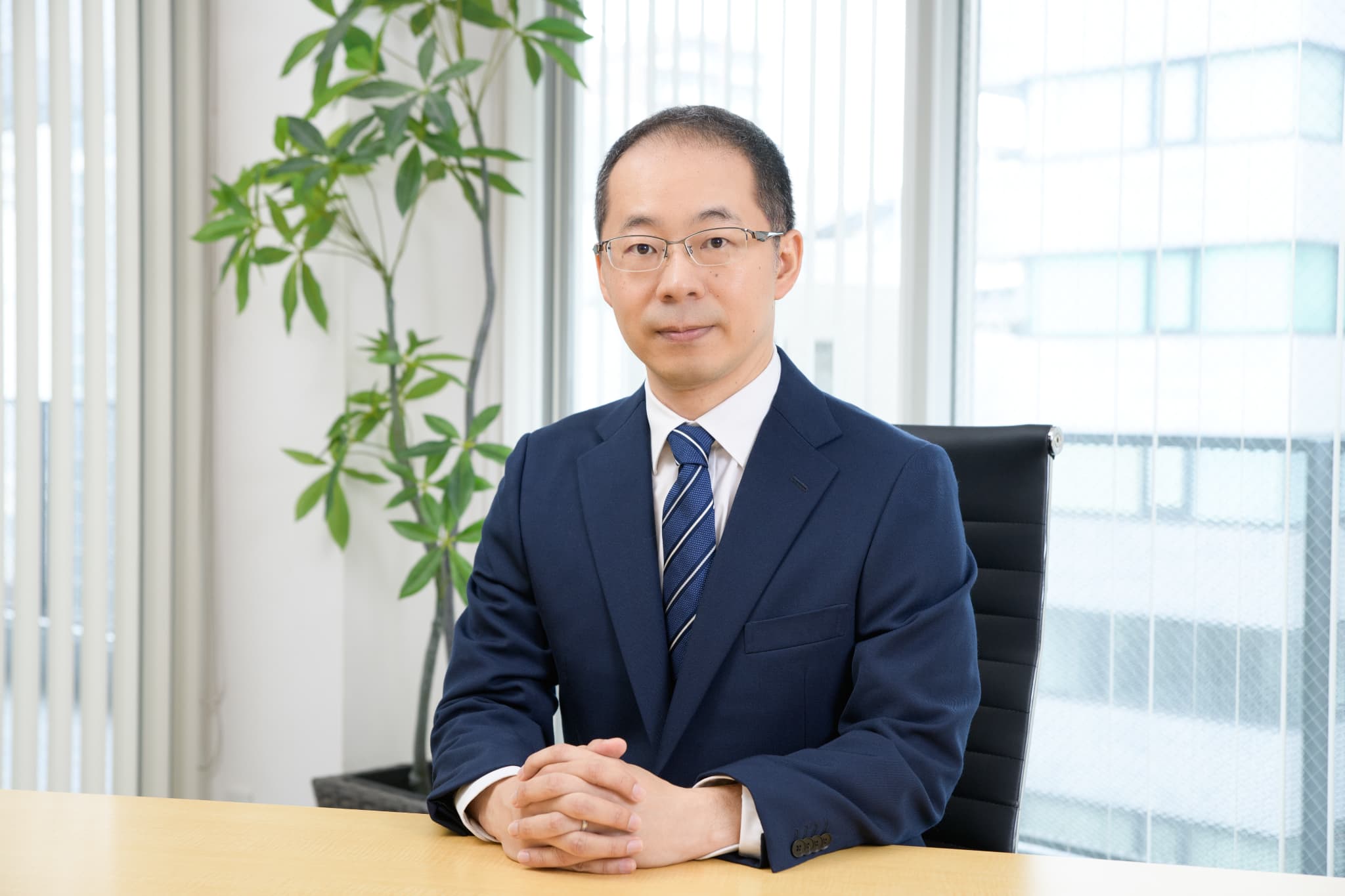
長年IATF 16949の審査を担当していますが、保全活動の形骸化や認証取得後の運用不備が原因で、想定外のトラブルに直面している現場を数多く見てきました。しかし、しっかりとTPMの考え方を取り入れた保全体制を構築できれば、故障ゼロ・不良ゼロに近づき、結果的には売上拡大・ブランド向上にも大きく貢献します。
お役立ち情報をお届けするまで」もぜひご覧ください。
記事作成のポリシーや工程については、「先に内容をまとめると以下となります。
- IATF 16949のTPMを活用して競争優位に
IATF 16949のTPMの管理の有効性を高め活用することで、認証以上の価値を生み出します。設備トラブルや品質不良を減らし、安定稼働と製品品質の向上を実現しましょう。 - 「保全」の強化で生産ロスとコストを削減
予防保全・予知保全を計画的に実施し、事後保全に頼らない体制を築けば、突発故障や修理費を大幅にカットできます。結果として、納期遵守率や収益性も向上します。 - 自己保全(自主保全)の導入で現場力アップ
作業者が日常点検や清掃を行うことで、小さな異常を早期発見し、品質意識を高められます。IATF 16949の“保全資源の提供”にも効果的です。 - KPI設定で改善サイクルを“見える化”
不良率・クレーム件数・OEE・MTBFなどを定期レビューし、未達時には標準作業や保全計画を見直します。数字の“見える化”により、経営層と現場が同じ目線で迅速に改善できます。 - 全社的な保全文化の構築が鍵
保全部門だけでなく、経営層や作業者を巻き込み、不良ゼロ・故障ゼロを目指します。当社のコンサル・トレーニング・内部監査支援も活用し、長期的な体質改善と組織力強化を図りましょう。
当社の詳細については、「会社概要」でご紹介しておりますので、ご興味があれば併せてご覧ください。
では、ここから詳しく見ていきましょう。
IATF 16949とTPM実践の意義
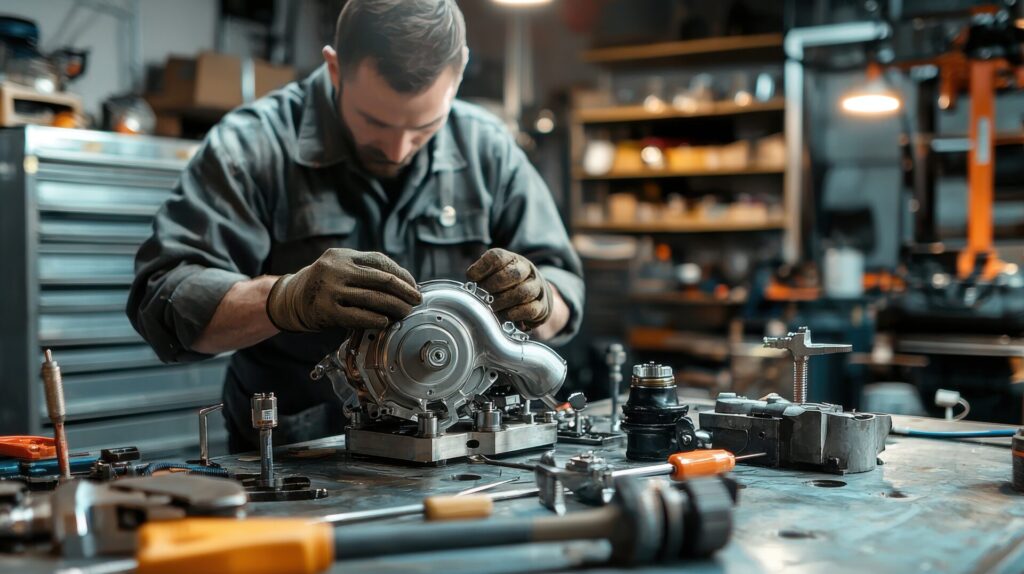
IATF 16949とは
IATF 16949は、自動車部品サプライヤー向けの品質マネジメント規格です。設備保全の強化や治工具管理などを厳密に求め、故障や不良率を減らすことを目的としています。
- 8.5.1.5 設備管理
- 8.5.1.6 治工具管理
これらの項目では、設備の稼働状況を安定させ、品質不良や納期遅延を防止するための保全計画を策定することが必須要件として提示されています。
TPMとの関連性
TPM(Total Productive Maintenance)は、設備故障ゼロ・不良ゼロを目指す“全員参加の生産保全活動”です。予防保全や予知保全、自主保全などを組み合わせて実施し、設備管理を体系的に進めることで、IATF 16949の要求事項をしっかり満たすと同時に、現場力の向上・生産コストの削減・品質安定といった成果を得られます。
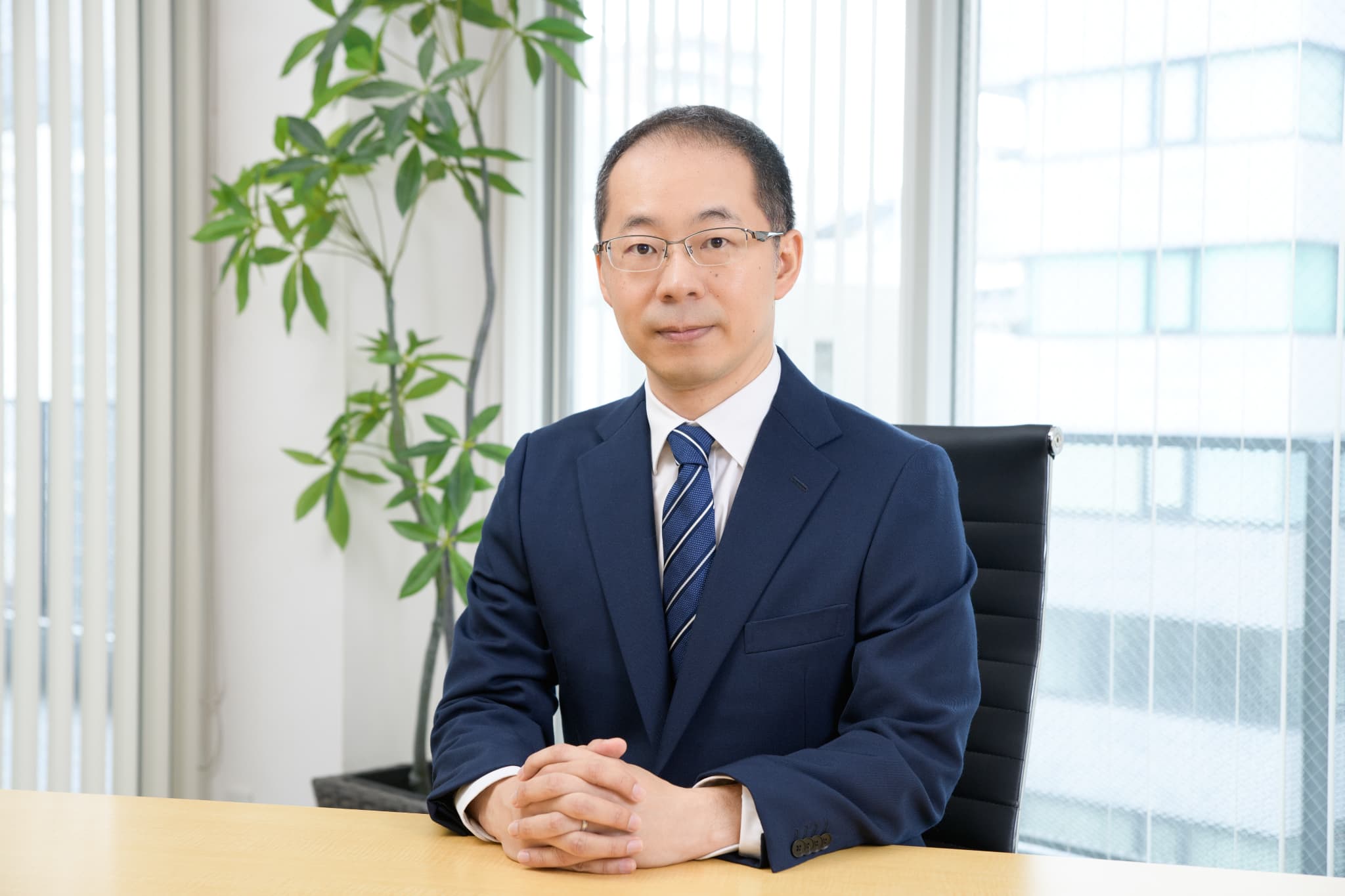
IATF 16949の審査現場でも、TPMの管理レベルが大きな差を生むと感じています。TPMをしっかり回せている企業は、故障率・不良率が確実に下がっています。
「保全」とは何か?
設備の長寿命化と生産性向上を両立する活動
製造現場における「保全」とは、設備を良好な状態に維持し、生産ロスを最小限に抑えるための活動全般を指します。具体的には、以下のような取り組みがあります。
- 予防保全(Preventive Maintenance)
設備を定期的に点検・整備し、計画的に消耗部品を交換することで故障を未然に防ぐ。 - 予知保全(Predictive Maintenance)
振動や温度などのセンサー情報を活用し、設備の異常兆候を事前に検知して保全を行う。 - 事後保全(Breakdown Maintenance)
故障が起きてから修理・交換対応を行う。なるべく予防保全や予知保全へ移行し、突発停止を減らすのが理想。
IATF 16949では、これらの保全活動が標準化・文書化され、計画的に実施されていることが求められます。自動車部品メーカーにとって設備の長寿命化と安定稼働は、コスト削減や納期遵守、品質安定に直結するため、保全強化は企業競争力の要と言えます。
「自己保全(自主保全)」とは?
現場作業者が点検や手入れを行う仕組み
「自己保全(自主保全)」は、現場オペレーターや作業員が自分の使う設備を日常的に点検・清掃し、簡単な修理や注油などを行う活動を指します。TPMにおいて特に重要な柱の一つであり、以下のようなメリットがあります。
- 異常の早期発見
ボルトの緩みや異音、油漏れなど、小さな兆候をいち早く見つけ対応し、大きな故障を未然に防ぐ。 - 作業者のスキル向上と品質意識の醸成
設備の仕組みを理解しやすくなり、品質や安全への意識が高まる。 - 生産ロスの削減
突発的な設備停止が減少し、計画外のダウンタイムを最小化できる。
IATF 16949では保全資源の提供(8.5.1.5 c)を求めており、必要な工具や教育が整ったうえで現場作業者が自主保全を行うことは、設備の安定稼働に大きく寄与します。
IATF 16949が求める保全活動とTPMの実践ポイント
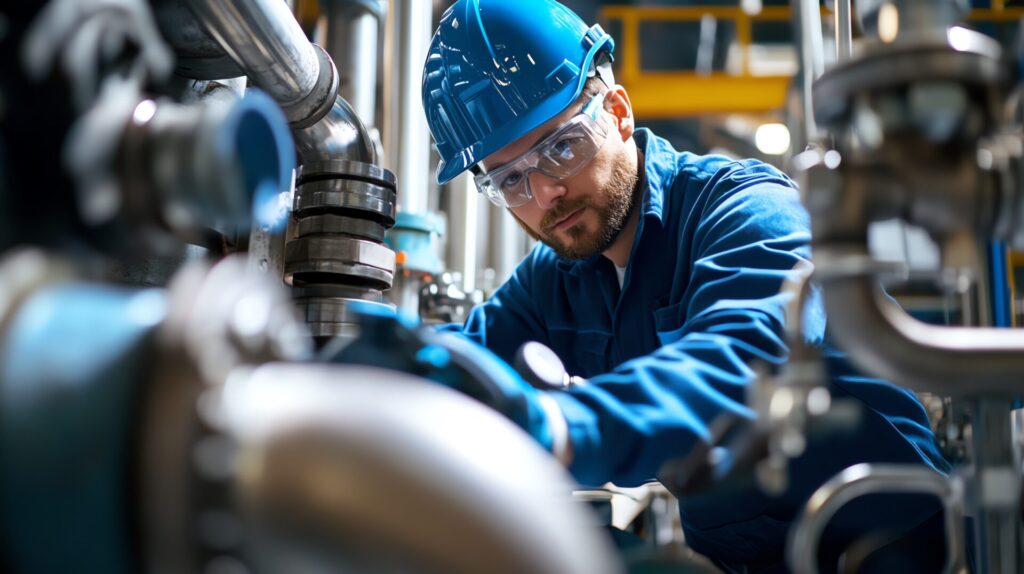
具体的な要求事項と対応策
IATF 16949の8.5.1.5(設備管理)や8.5.1.6(治工具管理)では、下記のような項目が要求されています。
- 必要な設備の特定(8.5.1.5 a)
- 設備リストアップ、優先度付け。
- 故障頻度や生産への影響度合いを考慮して保全計画を策定。
- 交換部品の確保(8.5.1.5 b)
- 消耗品の在庫切れを防ぎ、緊急時も迅速に対応できる仕組みを用意。
- 保全資源の提供(8.5.1.5 c)
- 人員、工具、予算などを適切に配分し、自主保全を含む保全活動を実行可能にする。
- 目標とモニタリング(8.5.1.5 f)
- OEE(設備総合効率)やMTBF(平均故障間隔)などKPIを設定し、継続的にレビュー。
- 予防保全・予知保全(8.5.1.5 h, i)
- 設備の定期点検や故障の兆候を捉える体制を作り、突発停止を最小化。
- 治工具の管理(8.5.1.6)
- 保管・交換スケジュールを文書化し、追跡性を確保。QRコードなどで使用履歴を管理。
全員参加によるTPM体制づくり
- 保全部門のみならず、経営層から現場オペレーターまで全員が保全に関与し、不良ゼロ・故障ゼロの目標を共有する。
- 自主保全や小集団活動を取り入れ、現場で発見した問題を素早く改善につなげる“現場力”を育成。
品質向上のためのKPI設定
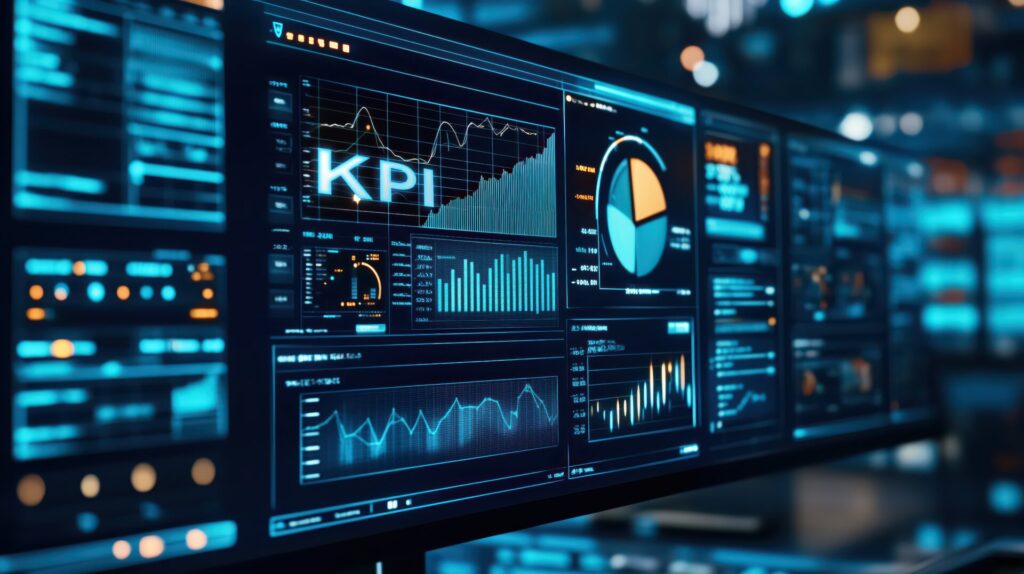
「見える化」で成果を共有し、継続的に改善
TPMやIATF 16949の導入効果を定量的に把握し、継続改善につなげるには、KPI(重要なパフォーマンス指標)の設定とモニタリングが欠かせません。よく採用される主なKPI例は以下のとおりです。
- 不良率(不良品発生率)
- 製造工程内・最終検査・顧客クレームまで、各段階での不良を把握。
- 目標値を設定し、削減策の効果を測定。
- 顧客クレーム件数
- 外部不良や返品の件数。顧客満足度に直結するため重要指標。
- OEE(設備総合効率)
- 稼働率(稼働時間の割合)×性能(目標速度比)×良品率(不良除外)で示される設備の総合指標。
- MTBF(平均故障間隔)/ MTTR(平均修復時間)
- 設備の信頼性や修理スピードを示す指標。
- 品質コスト
- 不良による手直し費用や部品廃棄、クレーム対応費などを定量化。
KPIは定期的にレビューし、その結果をもとに現場の標準手順や保全計画を見直すことが大切です。未達の場合は、小集団活動や標準作業の見直しなどを通じて対策を計画・実行し、目標に近づけていきます。
設備管理・保全手順マニュアル/標準書づくりのポイント

現行保全プロセスの可視化
- 設備一覧や点検周期、交換部品リストを“見える化”して整理し、過去トラブルの原因・対策も洗い出す。
- IATF 16949の8.5.1.5 a~cを満たすため、交換部品や保全資源の確保状況を文書化。
標準手順をマニュアルに組み込む
- マニュアル上で点検や予防保全のやり方を写真やイラストでわかりやすく説明。
- 自主保全に必要な簡易点検リストも用意し、「誰が・いつ・どの設備に・どんな点検をするか」 を明確にする。
治工具管理システムへの反映
- 治工具ごとに保管場所や交換サイクル、担当部署を明記し、追跡番号やQRコードなどでトレーサビリティを確保。
- 設計変更や改修時に、関連する文書を自動で更新できる仕組みを整備。
シンプルで使いやすい形にまとめる
- IATF 16949にのっとりつつも、複雑な手順書は現場で使われなくなるため、チェックリスト形式やフローチャートで可読性を高める。
- 紙運用とデジタル運用を併用して、作業者のレベルや設備台数・工場の規模に合った最適形にする。
点検記録や保守履歴フォーマットの作成ポイント
IATF 16949では、保全活動を実施した証拠(エビデンス)が要求されます。点検記録・保守履歴のフォーマットは次の点に注意しましょう。
- 必要データ項目を押さえる(8.5.1.5 f, g / 8.5.1.6 b, g)
- 設備名・識別番号、点検日、担当者、使用部品、異常の有無、是正処置など。
- 入力しやすさ・分析しやすさ
- チェックボックス+短いコメント欄で作業者が記入しやすいようにする。
- Excelやクラウド管理で自動集計できる形にすると、保全会議やKPIレビューがスムーズ。
- 識別情報の活用
- QRコードやバーコードを設備や治工具に貼り付け、履歴を即時に呼び出せるようにする。
次のステージへ – 認証取得以上の価値を生み出すには
IATF 16949は単なる「認証取得」や「お客様からの要求に対応する」だけではなく、自社の競争優位を築く絶好の機会になります。
- 高度な品質管理体制を整えることは、市場からの信頼獲得につながり、結果として新規ビジネスの拡大やブランド価値向上にも寄与します。
- 当社では、審査員としての視点+認証機関責任者としてのマネジメント経験を掛け合わせ、単なる手順や書類づくりだけで終わらない「経営戦略としての品質保証体制づくり」を支援しています。
当社が提供する総合サポート(一例)
- コンサルティングサービス: IATF 16949 / JIS Q 9100に精通した専門家が、認証取得からシステム構築まで支援。現場に負荷をかけずに運用できる仕組みをご提案します。
- トレーニングサービス: 自動車・航空機産業に特化した包括的な人材開発プログラム。短期的な認証対策から長期的な組織変革まで一貫してサポートします。
- 内部監査サービス: 現役のIATF審査員が内部監査を代行し、リスクを早期発見&改善提案。負荷を軽減しつつ認証維持の精度を高め、自社の品質競争力を向上させます。
- サプライヤーマネジメントサービス: IATF 16949 / JIS Q 9100のノウハウを活かし、サプライヤー監査や改善活動を総合的にサポート。品質不正リスクを早期に発見し、継続的な改善策を浸透させることで、サプライチェーン全体の品質とブランド価値を高めます。
当社の詳細については、「会社概要」からご覧いただけます。
「まずは無料で話を聞いてみたい」「認証取得のイメージを具体化したい」という方は、ぜひ初回30分の無料相談をご利用ください。
まとめ
- IATF 16949とTPMの融合で競争優位に
IATF 16949を満たすだけでなく、TPMを組み合わせることで、認証以上の価値を生み出します。設備トラブルや品質不良を減らし、安定稼働と製品品質の向上を実現しましょう。 - 「保全」の強化で生産ロスとコストを削減
予防保全・予知保全を計画的に実施し、事後保全に頼らない体制を築けば、突発故障や修理費を大幅にカットできます。結果として、納期遵守率や収益性も向上します。 - 自己保全(自主保全)の導入で現場力アップ
作業者が日常点検や清掃を行うことで、小さな異常を早期発見し、品質意識を高められます。**IATF 16949の“保全資源の提供”**にも効果的です。 - KPI設定で改善サイクルを“見える化”
不良率・クレーム件数・OEE・MTBFなどを定期レビューし、未達時には標準作業や保全計画を見直します。**数字の“見える化”**により、経営層と現場が同じ目線で迅速に改善できます。 - 全社的な保全文化の構築が鍵
保全部門だけでなく、経営層や作業者を巻き込み、不良ゼロ・故障ゼロを目指します。当社のコンサル・トレーニング・内部監査支援も活用し、長期的な体質改善と組織力強化を図りましょう。
IATF 16949に準拠したTPMの取り組みは、「不良ゼロ・故障ゼロ」を目指す最強の戦略です。保全部門だけでなく、経営陣や現場作業者を巻き込みながら、ぜひ一歩ずつ導入・定着を進めてみてください。結果的に、品質向上やコスト削減はもちろん、従業員のモチベーションアップといったプラス効果も期待できるでしょう。
IATF 16949でお悩みではありませんか?
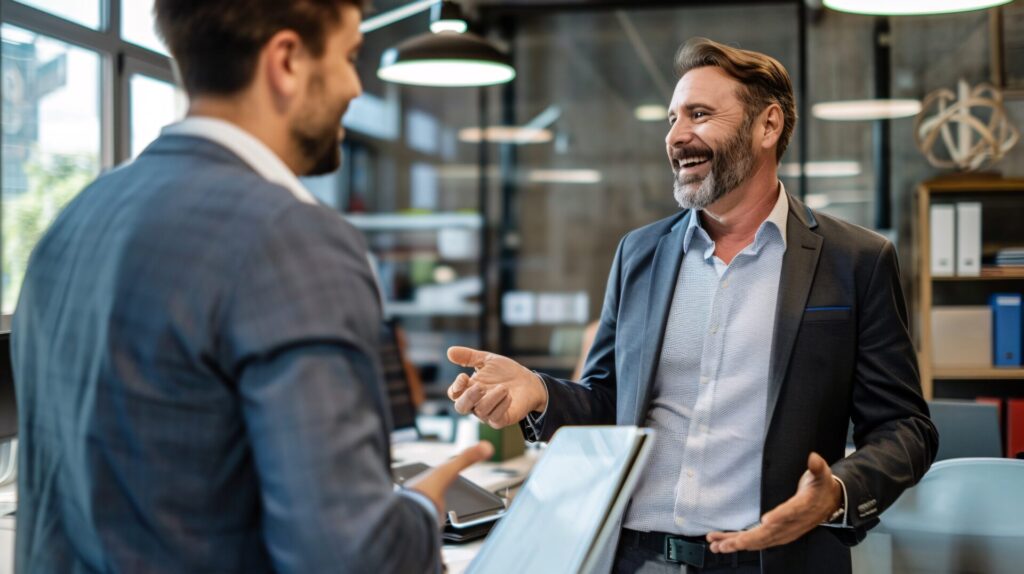
当社では、「認証取得」だけでなく、売上アップ・リスク低減・ブランド強化まで見据えたコンサルティングサービスを提供しています。顧客要求が厳しい自動車や航空機産業で数多くの経験に基づき、現場で負担なく運用できる仕組みづくりを徹底的にサポートいたします。
もし、「うちの現場にも当てはめたいけれど、具体的に何から着手すれば…?」とお悩みでしたら、ぜひ初回30分の無料相談をご利用ください。
当社の詳細については、「会社概要」からご覧いただけます。
さらに学びたい方へ
FMEAのポイントを押さえて、
品質リスクを
事前に防ぎませんか?
効果的なFMEAの作り方や
運用ノウハウをわかりやすく
解説しています。
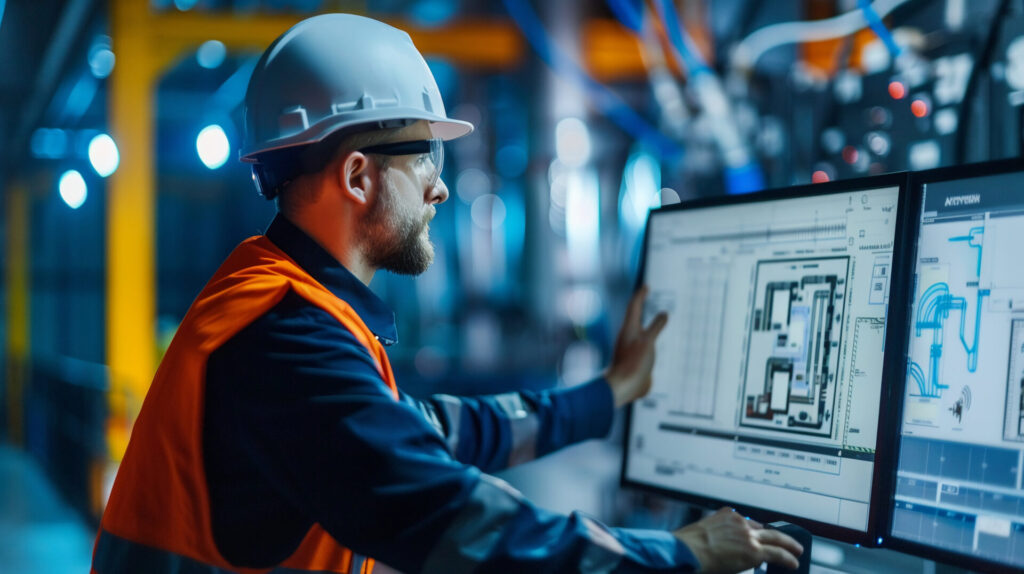
APQPの各フェーズを深く理解し、プロジェクト管理の精度を
高めませんか?
新製品立ち上げを
円滑に進める具体的な手法を、
初心者もわかりやすく学べます。
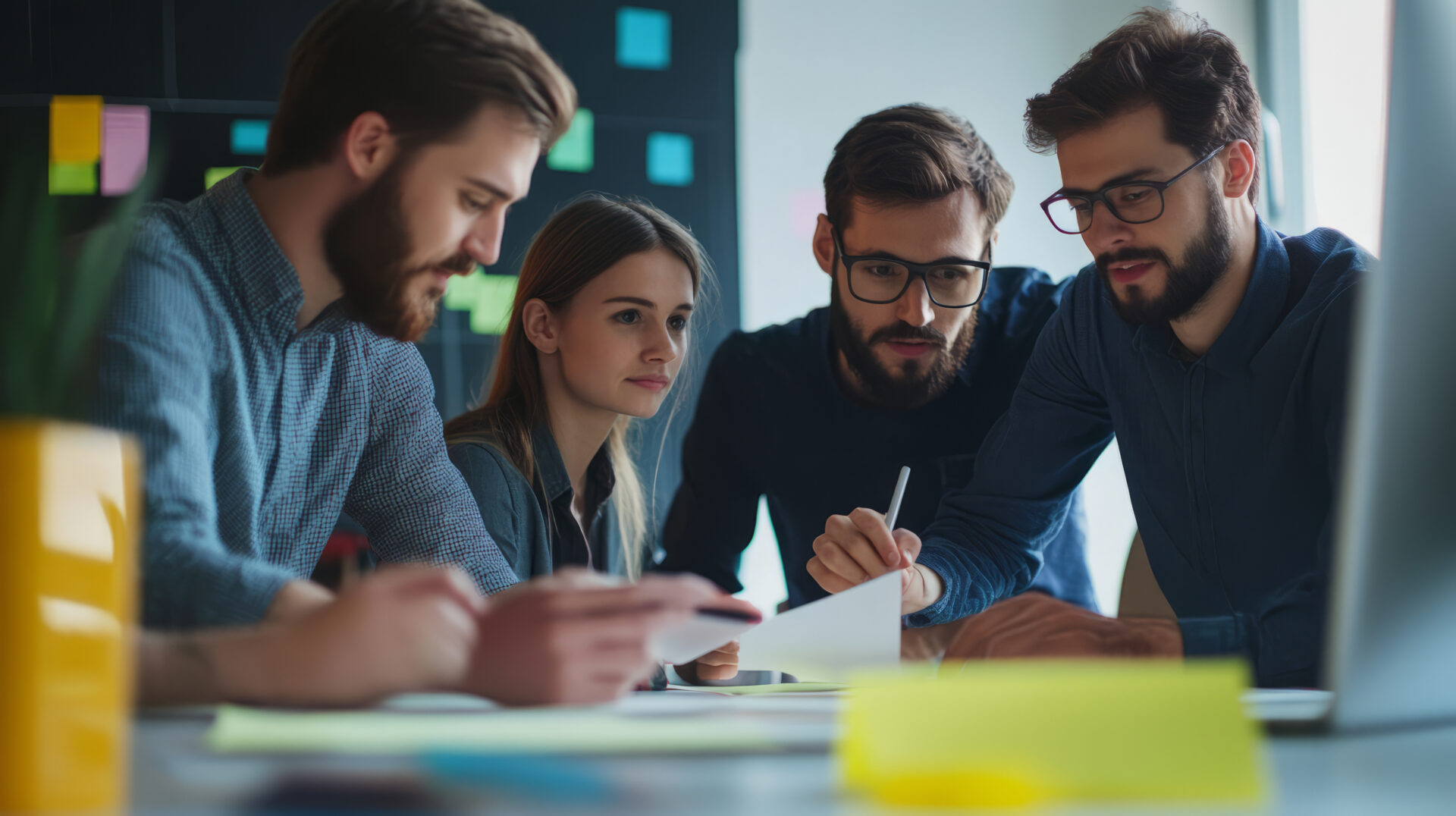
顧客からスムーズに承認されるコントロールプランの書き方を学びませんか?
実運用を踏まえて、コントロールプランの作成ポイントをわかりやすく解説しています。
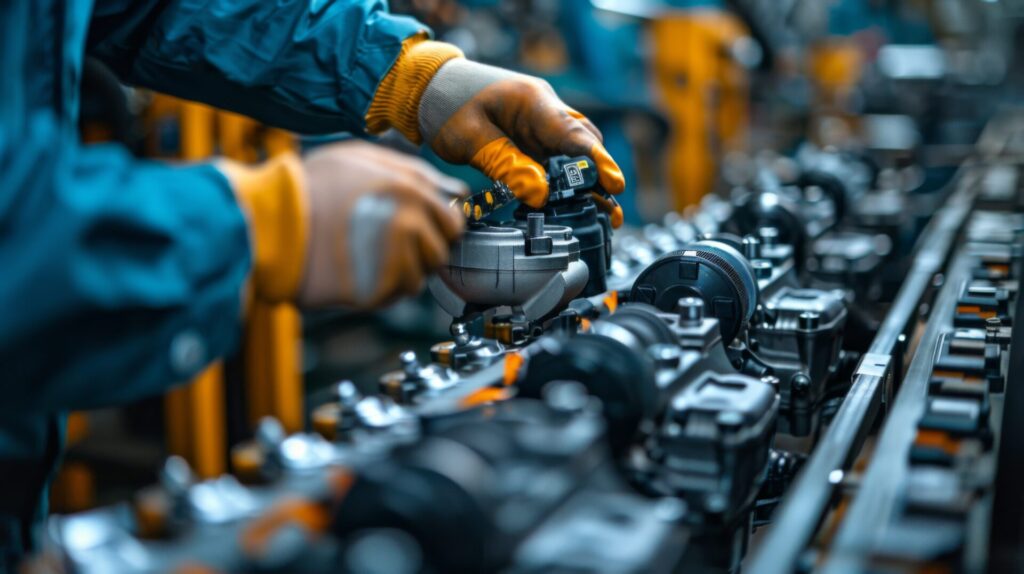
IATF 16949やJIS Q 9100に関する【お役立ち情報】を、他にも多数ご用意しています。
わかりやすい解説や、役立つノウハウを多数掲載していますので、ぜひ以下のページもご覧ください。
お役立ち情報一覧」を見る