特殊特性の管理を攻略する!IATF 16949の実践ガイドライン
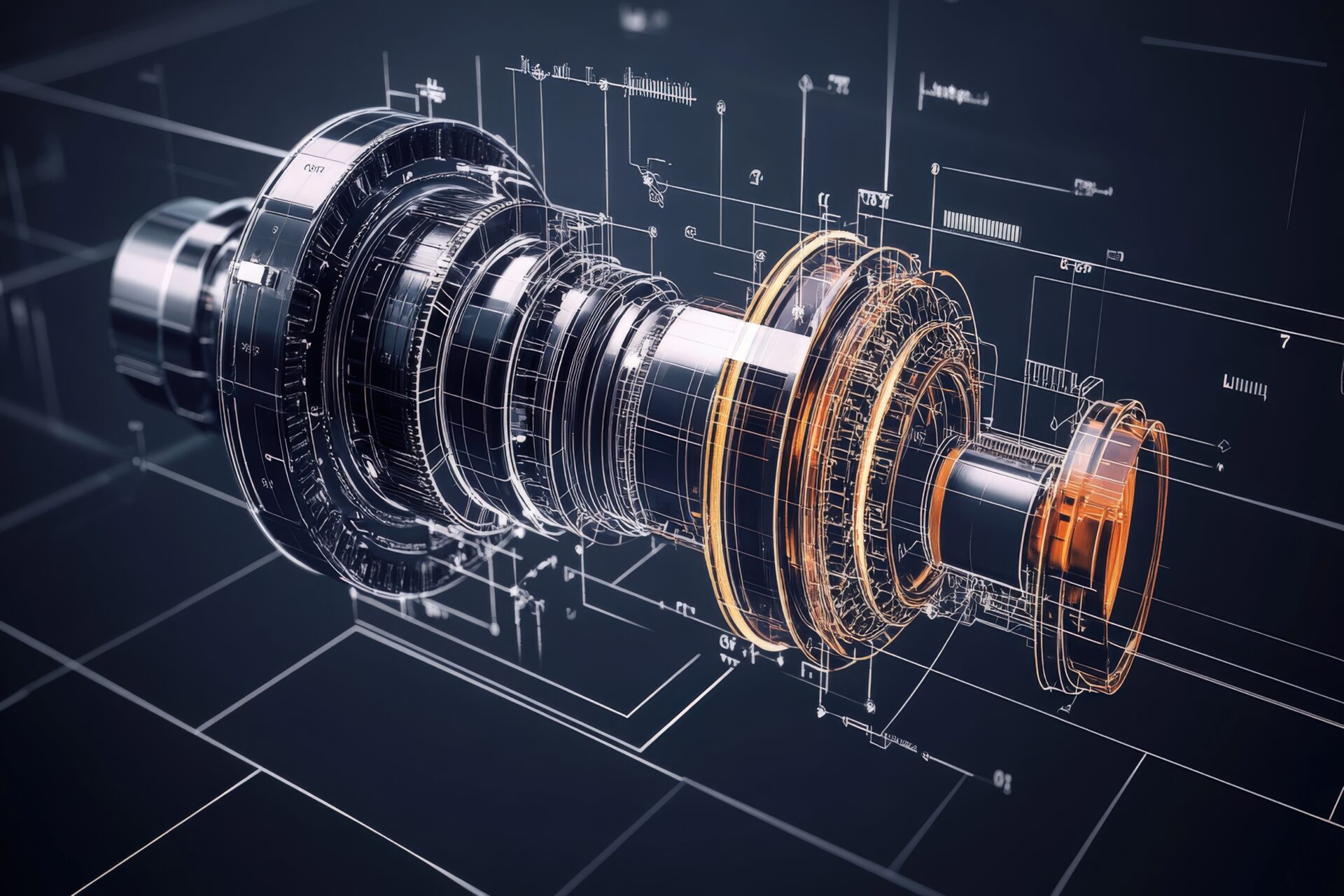
はじめに
この記事は、IATF 16949で要求されている特殊特性の管理において、以下のような疑問や不安を抱えている方向けに作られています。
- 「IATF 16949で“特殊特性”が重要だと聞くけれど、正直どのように管理するのが良いのか分からない」
- 「FMEAやコントロールプランなど、必要な手順や書類が多すぎて、整合性が取れなくなりそうで不安…」
- 「顧客から“特殊特性”として指定されたけど、うちの管理方法で本に大丈夫なのか…?」
もしこうした悩みをお持ちなら、それはあなただけではありません。特殊特性は製品の品質や安全性に直結するため、IATF 16949でも厳しい管理が求められる一方、顧客ごとの要求や社内の複雑な事情などが絡み合い、誰もがスムーズに対応できるわけではないのが現実です。
あなたも同じような悩みをお持ちでありませんか?
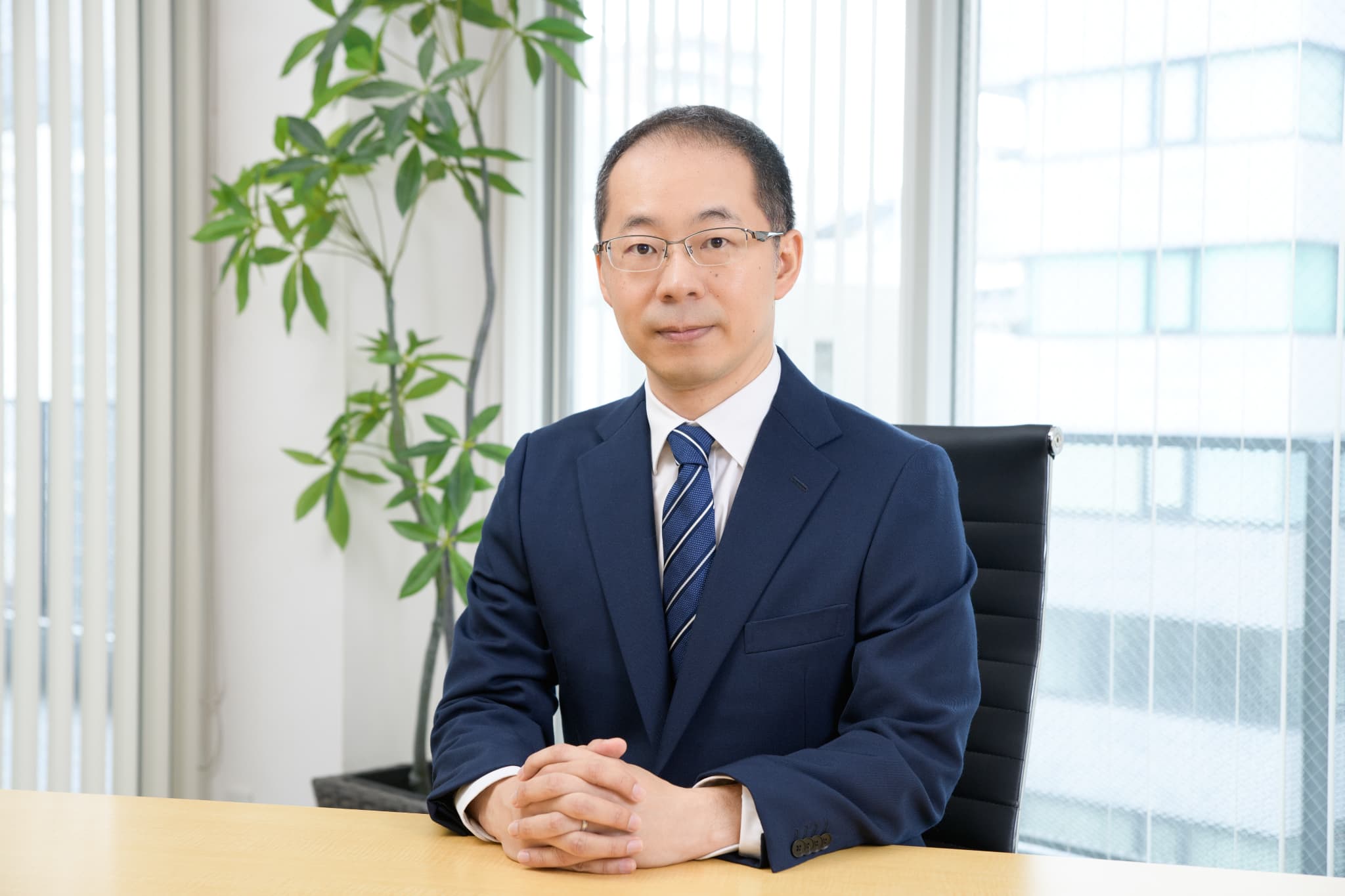
IATF 16949では、特殊特性の管理が不十分だと品質リスクにつながります。実際、特殊特性の選定・管理が甘いばかりに後々の不具合や是正処置に追われているケースを見かけます。最初にしっかりと基盤を整えておくことが大切です。
そこで、本記事では、現役のIATF 16949審査員資格を有する当社代表が、特殊特性管理の全体像を整理しつつ、具体的なステップを示すことで「どこからどう始めればいいのか」「どのように社内で共有・運用すればよいのか」を分かりやすく解説します。
お役立ち情報をお届けするまで」もぜひご覧ください。
記事作成のポリシーや工程については、「先にまとめると以下となります。
- 特殊特性の理解と把握
- 特殊特性とは、製品の品質・信頼性を左右する特性や工程パラメータを指し、設計段階から明確に定義・分類することで、重要度の高い領域を的確に管理できます。
- 顧客要求とリスク分析による特定
- 顧客が指定する特殊特性を正しく把握し、リスク分析(FMEAなど)を活用して、重大度・発生頻度・検出可能性が高い特性を抽出します。ここで見落としがあると、重大な不具合やリコールにつながるリスクが高まります。
- 設計段階でのアウトプット確認
- 図面・仕様書、DFMEA、PFMEAなどの設計アウトプットをしっかりレビューし、製品が求める機能や安全性、法規制との適合性を早期に把握することが、後工程でのコスト増大や品質リスクを抑えるカギです。
- 特殊特性の管理方法
- 特殊特性リストの確定
- 各部門が協力して優先度の高い特性をリスト化し、後のコントロールプランや標準作業手順書へ確実に反映します。
- 記号変換表の作成・運用
- 顧客ごとに異なる特殊特性の定義や記号を、社内でわかりやすく統一することで情報伝達ミスを防ぎ、品質管理の一貫性を保ちます。
- コントロールプランの作成
- 誰が、いつ、どのように特性を管理・監視するかを明確にし、不具合を未然に防止するための“ルールブック”として活用します。
- 標準作業手順書の整備
- 現場の作業手順を統一し、作業者の属人的なばらつきを低減。新人教育や要員交代時のスムーズな引き継ぎにも有効です。
- 特殊特性リストの確定
当社の詳細については、「会社概要」でご紹介しておりますので、ご興味があれば併せてご覧ください。
『ここまで整備できるとは、やっぱり御社はすごい』と顧客から言ってもらえそうというイメージを持ちつつ、ぜひ最後までお読みください。
では、ここから詳しく見ていきましょう。
特殊特性の理解
特殊特性(Special Characteristics)とは
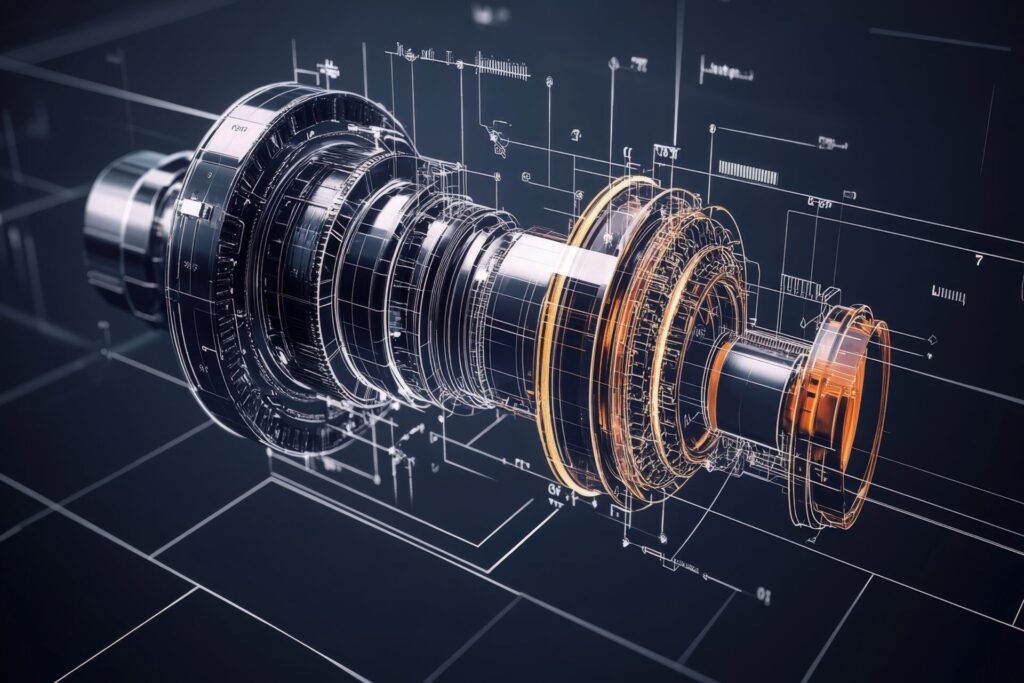
IATF 16949規格において、製品の安全性、規定への適合性、合わせ立て付け、機能、性能、その他の要求事項、または製品の後加工に影響を及ぼす可能性のある製品特性や製造工程パラメータのことを特殊特性と呼びます。これらの特性は、製品の品質や信頼性に直接的な影響を与えるため、正確に定義し分類することで、製品開発や製造プロセスにおいて重点的に管理すべき領域を明確にし、製品の品質と安全性を確保することが可能となります。
特殊特性の例:
- 安全性: 製品の使用中における、人の安全性に関わる特性(例:エアバッグの展開時間)。
- 規定適合: 法的・規制で決まっている項目への適合性(例:排出ガス基準)。
- 機能: 製品が意図された機能を果たすために必要な特性(例:ブレーキシステムの反応速度)。
- 性能: 製品の性能基準に関連する特性(例:エンジンの出力)。
- 後加工: 製品の組み立てや仕上げ工程に影響を与える特性(例:溶接部の強度)。
これらは品質や信頼性に直結するため、特に重点的な管理が必要とされています。ここをきちんと把握しておくと、顧客からの評価も上がりやすいのがポイントです。
IATF 16949の詳細については、以下の記事をご確認ください。
当社では、自動車・航空機産業に特化した豊富な現場経験から「特性の重要度やリスク度合いを正しく分類するノウハウ」を蓄積しています。現場レベルでも運用しやすい形で、特殊特性を管理するサポートが可能です。
特殊特性の特定プロセス
顧客要求事項の理解と反映
IATF 16949では、顧客が指定する特殊特性に対して組織が確実に対応することを求めています(IATF 16949:2016 8.2.3.1.2 参照)。
顧客指定の特殊特性を正確に把握できていないと、顧客が求める品質や機能、安全性が担保されません。結果としてクレームや返品、最悪の場合は事故やリコールにつながるリスクがあります。顧客指定の特殊特性を早期に把握し、内部管理に反映させることが重要です。
顧客との打ち合わせや要求仕様書を通じて、以下の情報を入手・分析します。
- 顧客図面上の特殊記号: 顧客が定める重要度や管理レベルを示す記号(例:CC(Critical Characteristic)等)
- 顧客コントロールプラン: 特殊特性を含む管理項目や管理手段
- 契約書や技術仕様書: 量産時の品質保証体制や検査基準に関する合意事項
リスク分析
IATF 16949ではリスク分析によって、製品や工程に内在するリスクを洗い出し、評価することで特殊特性を特定します(IATF 16949:2016 8.3.3.3 参照)。
リスク分析を省略したり不十分なまま特殊特性を設定してしまうと、本来管理すべきリスクを見逃してしまう可能性が高まります。
ここでは、代表的な手法であるFMEA(Failure Mode and Effects Analysis)を中心に、リスク分析のステップとポイントを解説します。
FMEAとは故障モードとその影響度・発生頻度・検出可能性を定量的に分析・評価し、対応を検討する手法です。FMEAを活用することで、不具合の発生頻度や影響度を定量化し、効率的かつ効果的に重要な特性に集中して対策を打つことができます。
リスク分析のステップ
1. リスクの洗い出し
- 潜在不具合モードの抽出
製品や工程における故障モード・不具合モードをリストアップします。- 例:部品寸法のズレ、強度不足、組付けミス、設備故障、人的エラー など
- 部門横断的アプローチの重要性
設計・製造・品質・購買など、多様な部署が参加してリスクを網羅することで、見落としや偏りを防ぎます。
2.リスクの評価(FMEA)
- FMEA(Failure Mode and Effects Analysis)の概要
不具合が与える影響の大きさ(重大度:S)、起こりやすさ(発生頻度:O)、そして発生した不具合を検出できる可能性(検出可能性:D)を数値化し、リスクを客観的に評価します。 - 優先度の明確化
RPN(Risk Priority Number)を用いて、管理すべきリスクの優先順位を決定します。- 例:安全性や法規適合に直結する特性は最優先管理が必要。
3.特殊特性の抽出
- コントロールプランや標準作業手順書との連携
抽出した特殊特性は、後の工程設計・製造管理で重点的に監視・制御するため、コントロールプランや標準作業手順書に展開されます。主に以下のアプローチが用いられます。 - 重大リスクへの対策
リスク評価の結果、重大度が高い、または発生頻度が高い、あるいは検出しにくい不具合モードを抑えるために重要となる特性を「特殊特性」として設定します。
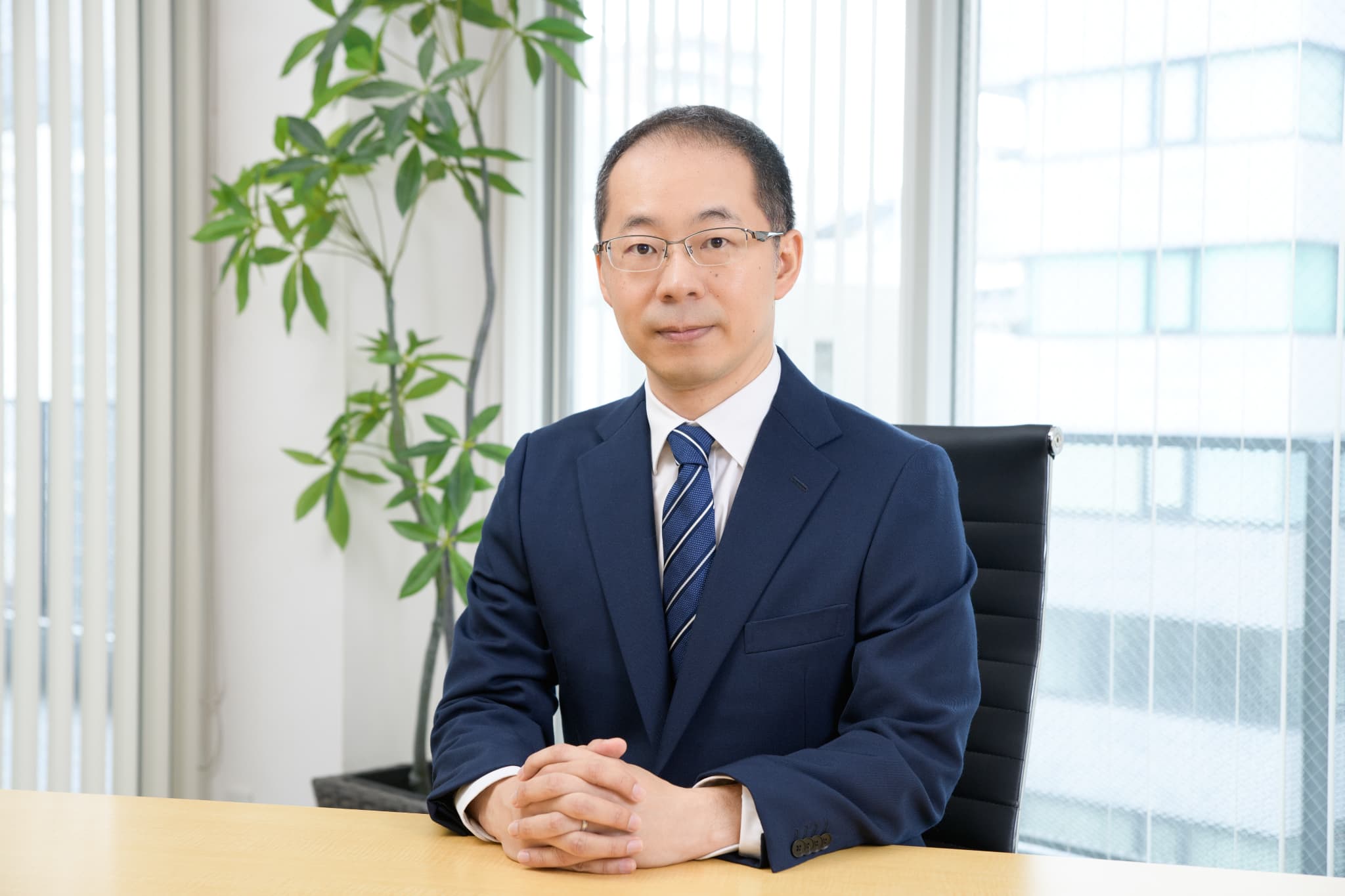
FMEAを形式的にやって終わりにする組織もありますが、最終的に抽出された特殊特性を実際のコントロールプランまで落とし込み、一貫して運用することがポイントです。管理対象をしっかり絞り込むことで、結果的にはコスト削減やリスク低減につながります。
設計からのアウトプット
IATF 16949では、設計段階から特殊特性を特定することが要求されています(IATF 16949:2016 8.3.5.2 参照)。
設計段階で特殊特性を見落とすと、後工程での修正コストや品質リスクが大幅に増大します。設計段階のアウトプットをしっかり確認することで、製品が求められる機能や安全性、法規制への適合性などを把握し、特殊特性を管理するシステムをつくることができます。
以下のような文書やデータが設計からのアウトプットに含まれ、これらのアウトプットには特殊特性が識別されていることが求められています。
- 図面・仕様書: 製品の形状や寸法、材料、許容誤差などを示す基本ドキュメント
- 設計FMEA(DFMEA):製品設計段階で想定される故障モードとその影響を分析し、対策を検討する文書
- 工程FMEA(PFMEA):製造・組立工程で発生し得る故障モードを分析し、その原因・影響を明確化する文書
- コントロールプラン:特殊特性を含めた製造工程で管理する特性をどのように監視・管理するかをまとめた計画書
- 標準作業手順書:製造現場における作業手順や注意点を記載し、設計意図に沿った組立や検査を現場レベルで再現できるようにする文書
特殊特性の管理方法
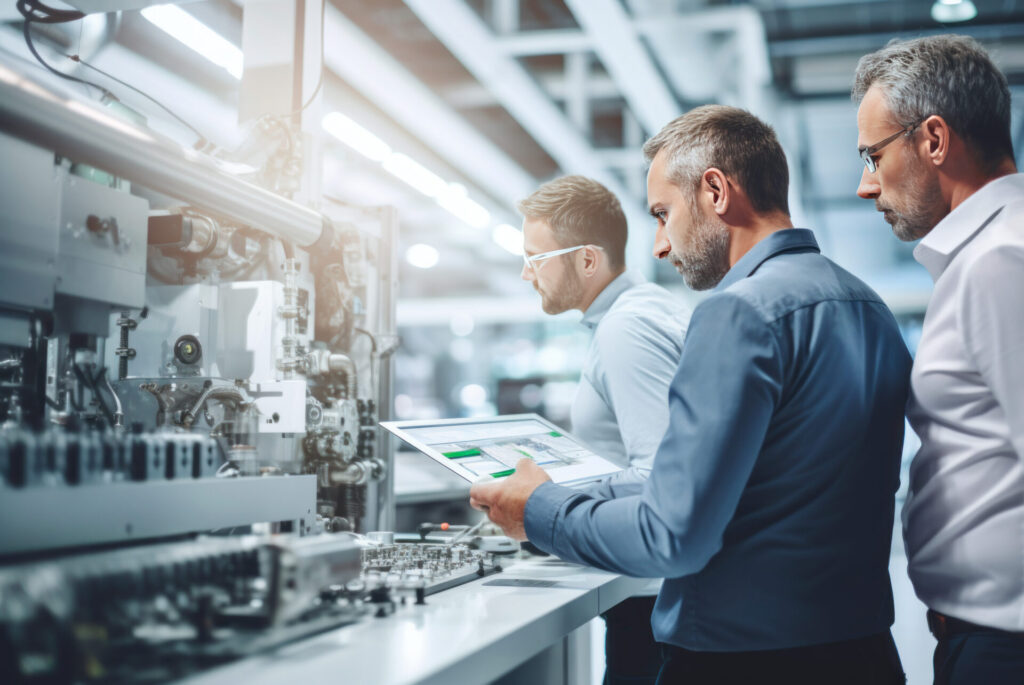
特殊特性リストの確定
前項(特殊特性の特定プロセス)で特定・優先順位付けした特殊特性を、管理業務の前段階としてリスト化し、明確に可視化するステップです。製品開発・工程設計・品質管理などの各部門が協力し、どの特性をどう管理するか、全社的に共有できる仕組みを整えます。
リスト化することで、何を優先的に管理すべきか全員が明確に把握でき、後の工程設計や教育にもスムーズに活かすことができます。また、特殊特性を具体的なリストとして確定しておかないと、後の管理プロセス(コントロールプランや標準作業手順書の整備など)において「どの特性を管理すべきか」曖昧になりやすくなります。明確なリストを作成しておくことで、担当部署や作業者が共通認識を持ち、抜け漏れなく的確に管理を進めることが可能になります。
特殊特性リストに含めるべき主な項目:
- 特性名: 設計図面や仕様書で定義される特性の名称
- 根拠・重要度: なぜ特殊特性なのか、どの程度の重要度かを示す
- 管理対象箇所: 対象となる図面番号、工程名、または設備名
- 許容範囲・規格値: 顧客要求値、社内基準など
- 検査方法・測定機器: 後段のコントロールプランで参照する管理手段の概要
- 備考: 顧客の指定や特記事項、注意点など
記号変換表の作成と管理
IATF 16949の要求事項には、顧客が定義した特殊記号や表記法を、組織独自の記号に置き換える場合に「記号変換表」を用いることが要求されています(8.3.3.3 d) 参照)。
これは顧客から提示される特殊特性の情報を正しく認識し、組織内でも混乱なく共有するための手段です。
顧客独自の記号や表記法をそのまま使う場合、社内の他部署や他製造拠点で混乱が起こる可能性があります。記号変換表を作成することで、顧客要求を確実に満たしつつ、社内の統一された管理ルールを維持することが可能になります。これにより、情報伝達ミスを防ぎ、品質管理の一貫性を保つことができます。
記号変換表の例
顧客 | 顧客記号 | 顧客定義 | 組織内記号 | 組織内定義 |
顧客A | CC(Critical Characteristic) | 安全性・法規適合に直接影響し、不良発生時には重大事故や規制違反となる恐れが高い特性 | KCC (Key Critical Characteristic) | 安全面・法規面で最優先管理が必要な特性。100%検査もしくは高度な統計的工程管理を適用する。 |
顧客A | SC(Significant Characteristic) | 機能や性能に大きく影響し、不良が出ると顧客満足度の低下や市場クレームにつながる恐れがある特性 | KSC (Key Significant Characteristic) | 製品機能・顧客満足度に直接影響する特性。サンプリング検査やSPCを活用して管理する。 |
顧客B | SQ(Special Quality) | 製品性能や信頼性を左右する特性 | KSC (Key Significant Characteristic) | 製品機能・顧客満足度に直接影響する特性。サンプリング検査やSPCを活用して管理する。 |
- 顧客記号: 顧客が図面や仕様書で使用している特殊特性用の記号
- 顧客定義: 顧客が定める特性の意味や重要度
- 組織内記号: 組織が内部で管理しやすいように再定義した記号
- 組織内定義: 組織での運用・管理ルールの明確化
記号変換表を作成・運用するポイント
- バージョン管理と変更手順
顧客仕様の改訂や新規顧客の追加に対応できるよう、記号変換表にバージョン番号や更新日、改訂内容を明記し、最新情報を常に社内に周知する。 - 全社的な周知と教育
記号変換表は設計、製造、品質、購買、営業など、すべての関連部署が参照する。更新のたびに関係部署へ通知し、誤用や混乱を防ぐための教育を実施する。
変換表を作り、関係部署に周知・教育することで、情報伝達ミスを防止し、「現場が正しく理解できるように、きちんと配慮している」と評価されることにつながります。
コントロールプランの作成
コントロールプラン(Control Plan) は、特殊特性を含む製品・工程上の重要な管理項目を確実に監視・制御するための文書です。IATF 16949では、特に特殊特性に対する管理手段を明確化することが求められています(8.5.1.1 コントロールプラン 参照)。
コントロールプランがないと、誰が・いつ・どのように特殊特性を管理するかが曖昧になります。その結果、重要な特性を見落とし、品質トラブルや顧客クレームにつながるリスクが高まります。逆に、きちんと作成・運用されているコントロールプランは、製造現場の安定稼働と品質確保のための“ルールブック”として機能し、不具合の未然防止につながります。しっかりしたコントロールプランが運用されている企業は、「ルールが定着していて不良率が低いね」と顧客からの信頼度が高まる事例も多いです。
コントロールプランに含まれる主な管理項目:
- 特性: 製品特性や工程パラメータ(特殊特性の場合、それを示す識別を含む)
- 仕様・許容: 規格値や管理値(許容範囲)
- 方法: 管理や検査の方法・手順、工程装置や計測機器
- 評価・測定: 検査や計測の頻度、サンプリング数
- 対応計画: 不良が発生した場合の対処方法
コントロールプランの詳細については、以下をご確認ください。
標準作業手順書の整備
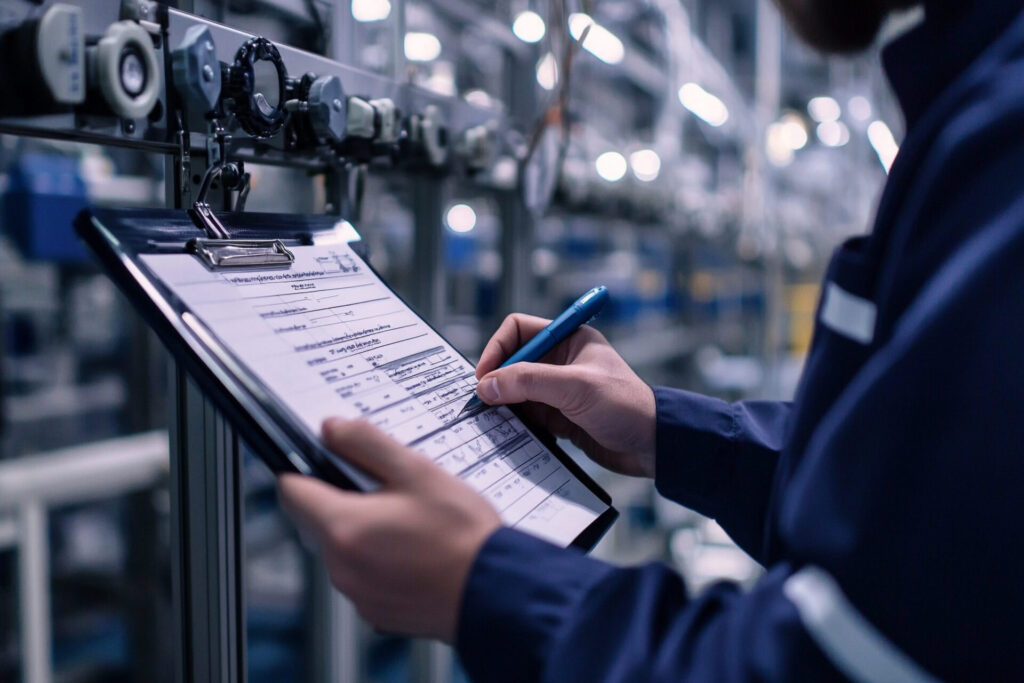
標準作業手順書は、作業者が一貫した品質を確保しながら作業を行うための指示書です。特殊特性に関する管理内容を作業手順書に明確に落とし込むことで、作業者が日常業務の中で確実に特性をコントロールできるようになります。
作業者が属人的に作業を行うと、特殊特性の管理にバラつきが生じ、不良発生率が上昇する恐れがあります。作用手順書を整備し、誰が作業しても同じ手順で進められるようにすることで、再現性の高い品質管理が可能になります。また、新人教育や代替要員の育成にも効果的で、現場のスキルレベルや生産性向上につながります。実際、「現場で使える標準化」ができている企業は、社内外から「品質管理レベルが高い」と認められる傾向が強いです。
標準作業手順書に含めるべきポイント:
- 作業手順: 特殊特性を管理するうえで重要となる操作やチェックポイント
- 使用する工具・計測機器: 測定器具の種類・設定方法、校正情報など
- 合否基準: 特殊特性に対して設定された許容範囲と判断基準
- 不良時の対応: 作業者が異常を検知した際の連絡先や処置方法
次のステージへ – 認証取得以上の価値を生み出すには
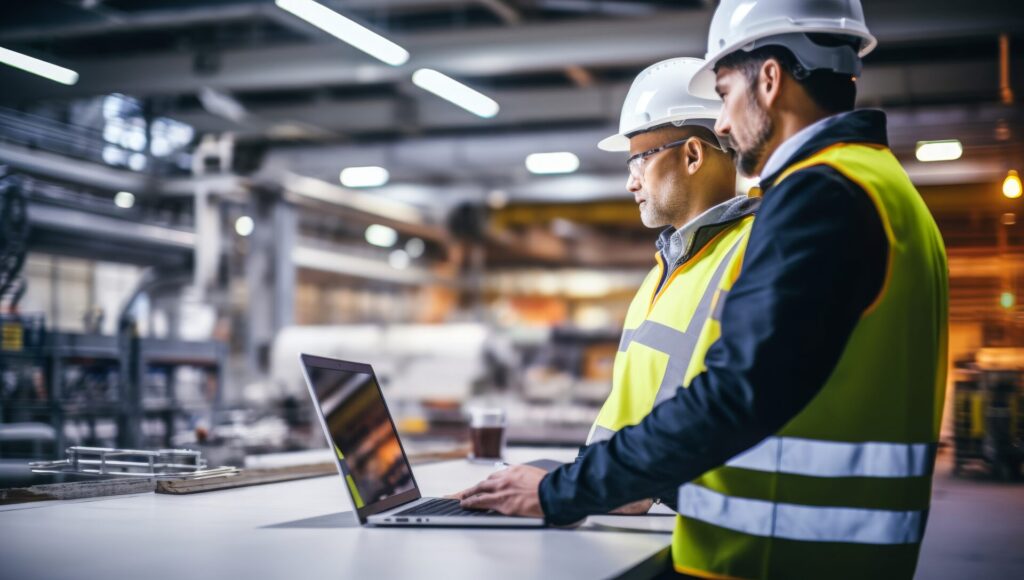
IATF 16949の導入は「お客様からの要求に対応する」だけではなく、自社の競争優位を築く絶好の機会になります。
- 品質管理体制を整えることは、市場からの信頼獲得につながり、結果として新規ビジネスの拡大やブランド価値向上にも寄与します。
- 当社では、審査員としての視点+認証機関責任者としてのマネジメント経験を掛け合わせ、単なる手順や書類づくりだけの「形だけの認証」で終わらない「経営戦略としての品質保証体制づくり」を支援しています。
- 認証を取った“後”の運用こそ本番。継続的改善が回り続ける仕組みを作り込むことで、不具合低減・コスト削減・ブランド向上などのメリットを最大限に活かせます。
当社では、以下のような総合サポートを行っています。
- コンサルティングサービス
- 審査員かつ認証機関責任者としての経験をフルに活かし、最短・最適な認証取得とリスク最小化を支援
- 「現場にフィットした品質マネジメントシステム」の構築で、品質をコアとした競争優位を確立
- 認証取得だけで終わらず、売上向上・リスク低減・ブランド強化の三拍子を狙える包括的な品質経営サポート
- トレーニングサービス
- 「机上の理論」に偏らず、実務レベルで使える内容を重視
- 企業文化を尊重しつつ、現場力を高める人材育成プログラムを提供
- IATF 16949への理解を深めながら、短期成果と長期的な企業価値向上を両立
- 内部監査サービス
- 現役の審査員が内部監査員としてアウトソーシング対応
- 担当者の作業負荷を大幅軽減し、外部審査での指摘リスクを最小化
- 監査員育成にも注力し、将来的に社内完結できる監査体制を構築
- サプライヤーマネジメントサービス
- 重大リスクを未然に防止し、サプライチェーン全体の品質基盤を強化
- 生産効率や納期も犠牲にせず、サプライヤーが自律的に改善を継続できる仕組みを構築
- 認証機関との連携も含め、一括でサポートし、OEM/Tier1の業務負担を大幅に軽減
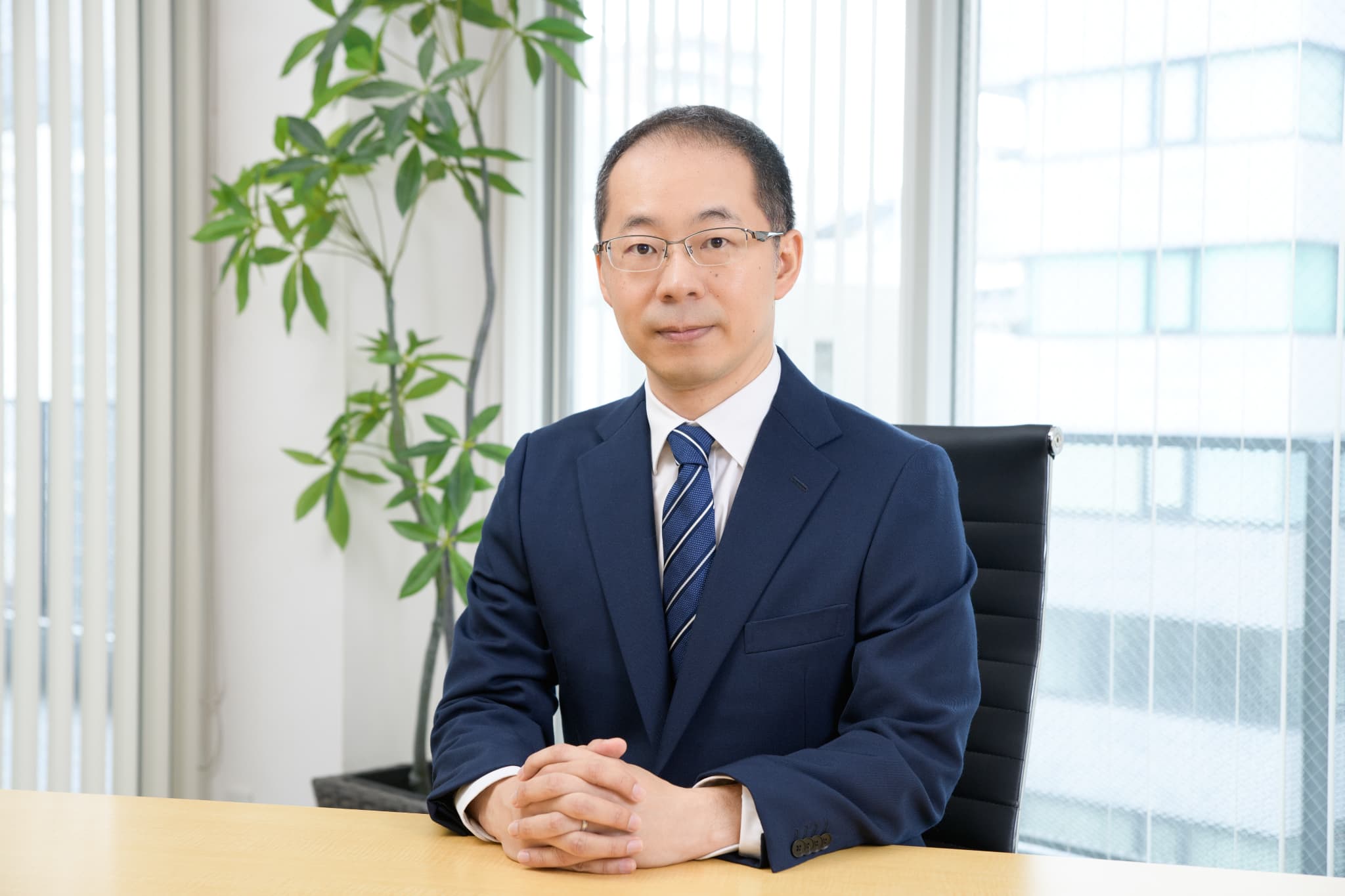
戦略的に競争優位を獲得することが重要な時代です。IATF 16949導入は“コスト”ではなく“投資”と考えて、長期的なリターンを最大化していきましょう。
当社の詳細については、「会社概要」からご覧いただけます。
今なら30分の無料相談を実施中
- 「どこから手をつければいい?」
- 「本当に自社に認証が必要?」
- 「どの程度の費用・期間がかかる?」
こうした疑問を抱えた方に向け、初回30分の無料オンライン相談を行っています。
30分の無料相談で解決できること
- 自社の現状把握と、必要なギャップ分析の進め方
- システム導入の具体的なイメージ
- 認証取得の手順・費用・期間の目安
- 運用定着や内部監査のサポート内容
まとめ
IATF 16949に準拠した特殊特性管理の考え方や手順を、特定から管理・評価の流れに沿って解説しました。
- 特殊特性の理解と把握
- 特殊特性とは、製品の品質・信頼性を左右する特性や工程パラメータを指し、設計段階から明確に定義・分類することで、重要度の高い領域を的確に管理できます。
- 顧客要求とリスク分析による特定
- 顧客が指定する特殊特性を正しく把握し、リスク分析(FMEAなど)を活用して、重大度・発生頻度・検出可能性が高い特性を抽出します。ここで見落としがあると、重大な不具合やリコールにつながるリスクが高まります。
- 設計段階でのアウトプット確認
- 図面・仕様書、DFMEA、PFMEAなどの設計アウトプットをしっかりレビューし、製品が求める機能や安全性、法規制との適合性を早期に把握することが、後工程でのコスト増大や品質リスクを抑えるカギです。
- 特殊特性の管理方法
- 特殊特性リストの確定
- 各部門が協力して優先度の高い特性をリスト化し、後のコントロールプランや標準作業手順書へ確実に反映します。
- 記号変換表の作成・運用
- 顧客ごとに異なる特殊特性の定義や記号を、社内でわかりやすく統一することで情報伝達ミスを防ぎ、品質管理の一貫性を保ちます。
- コントロールプランの作成
- 誰が、いつ、どのように特性を管理・監視するかを明確にし、不具合を未然に防止するための“ルールブック”として活用します。
- 標準作業手順書の整備
- 現場の作業手順を統一し、作業者の属人的なばらつきを低減。新人教育や要員交代時のスムーズな引き継ぎにも有効です。
- 特殊特性リストの確定
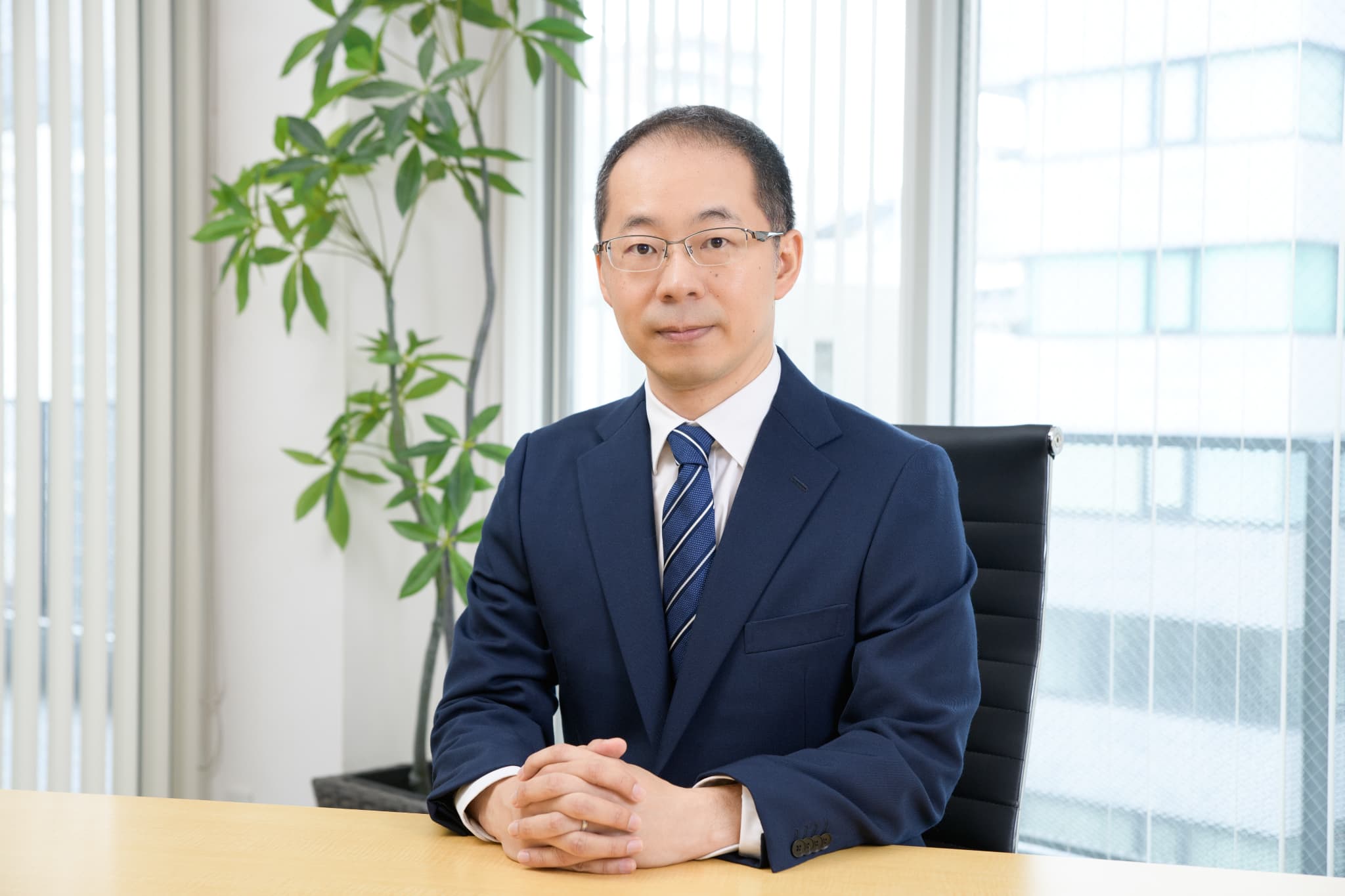
特殊特性は言わば“品質のかなめ”です。ここをしっかり管理できるかどうかで、長期的なブランド価値やビジネス拡大にも影響します。認証取得をゴールにせず、“品質”を競争優位に変えていきましょう。
IATF 16949や特殊特性でお悩みではありませんか?
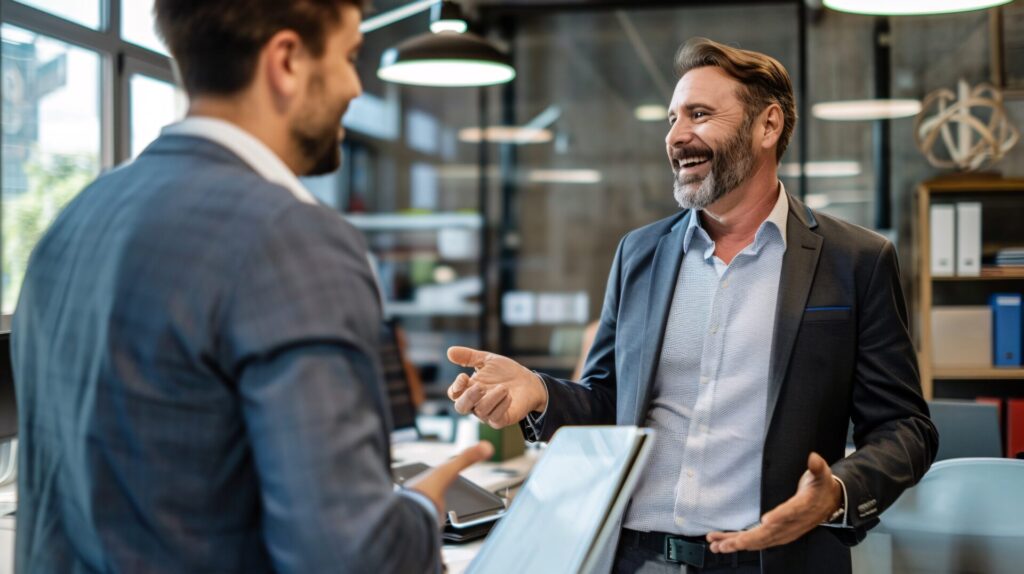
当社では、「認証取得」だけでなく、売上アップ・リスク低減・ブランド強化まで見据えたコンサルティングサービスを提供しています。顧客要求が厳しい自動車や航空機産業で数多くの経験に基づき、現場で負担なく運用できる仕組みづくりを徹底的にサポートいたします。
もし、「うちの現場にも当てはめたいけれど、具体的に何から着手すれば…?」とお悩みでしたら、ぜひ初回30分の無料相談をご利用ください。
当社の詳細については、「会社概要」からご覧いただけます。
さらに学びたい方へ
FMEAのポイントを押さえて、
品質リスクを
事前に防ぎませんか?
効果的なFMEAの作り方や
運用ノウハウをわかりやすく
解説しています。
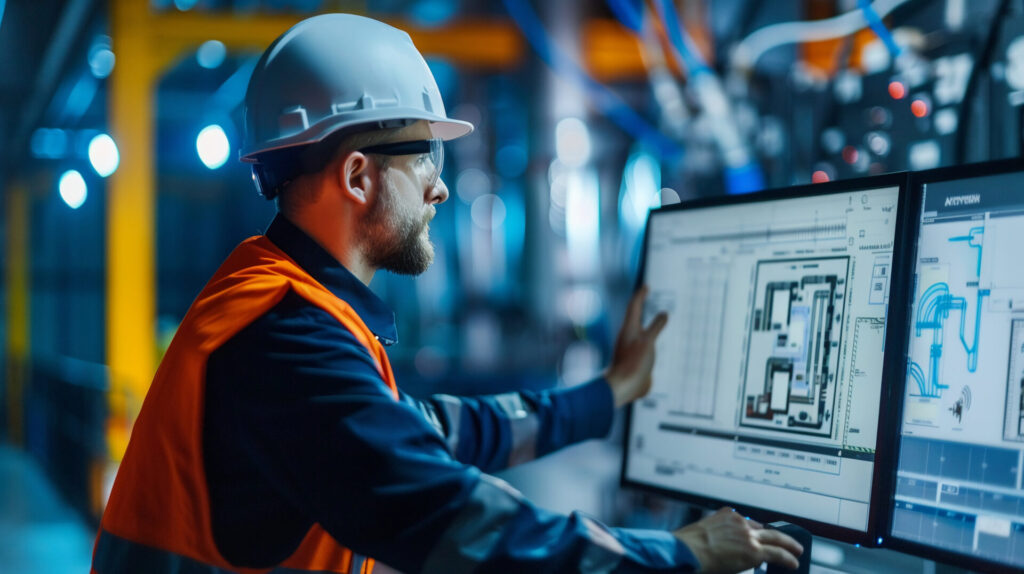
APQPの各フェーズを深く理解し
プロジェクト管理の精度を
高めませんか?
新製品立ち上げを
円滑に進める具体的な手法を、
初心者もわかりやすく学べます。
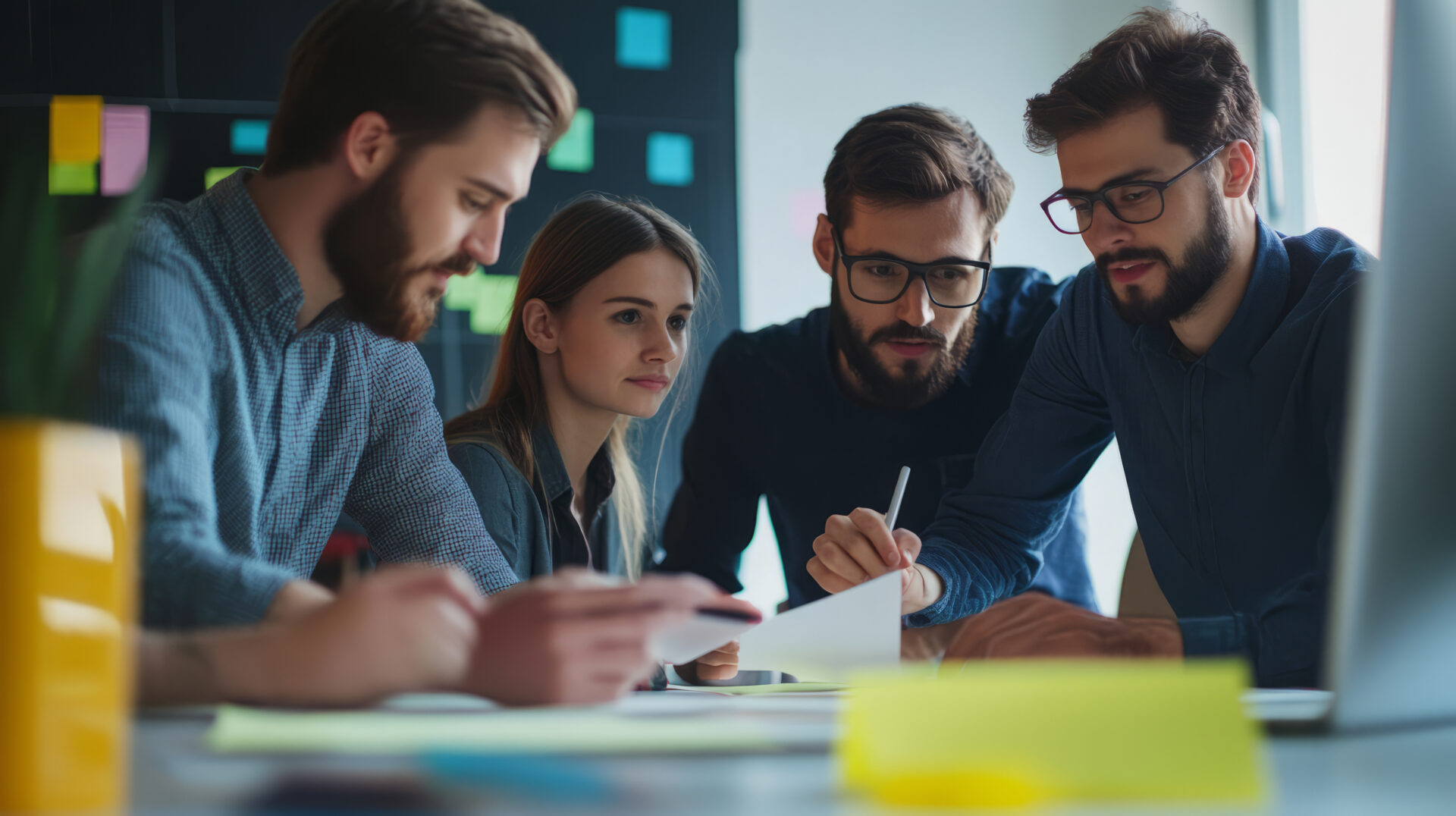
内部監査で是正処置の効果と有効性をしっかりと確認できていますか?
是正処置の有効性を検証する
内部監査の進め方を
分かりやすく解説しています。
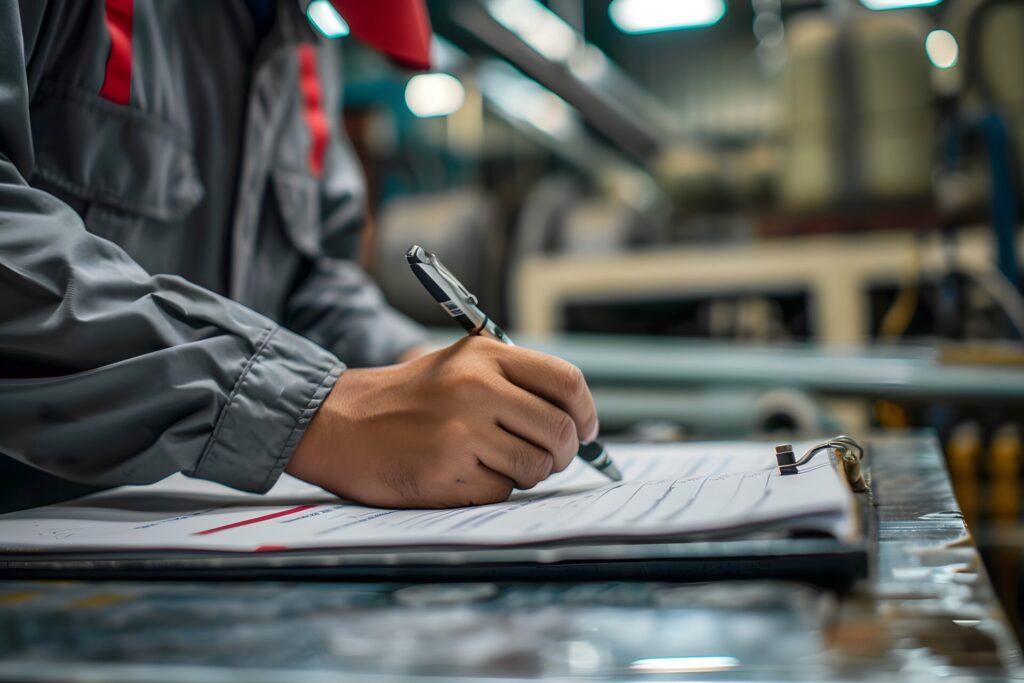
IATF 16949やJIS Q 9100に関する【お役立ち情報】を、他にも多数ご用意しています。
わかりやすい解説や、役立つノウハウを多数掲載していますので、ぜひ以下のページもご覧ください。
お役立ち情報一覧」を見る