IATF 16949のサプライヤーマネジメント 重要性と実践ポイント
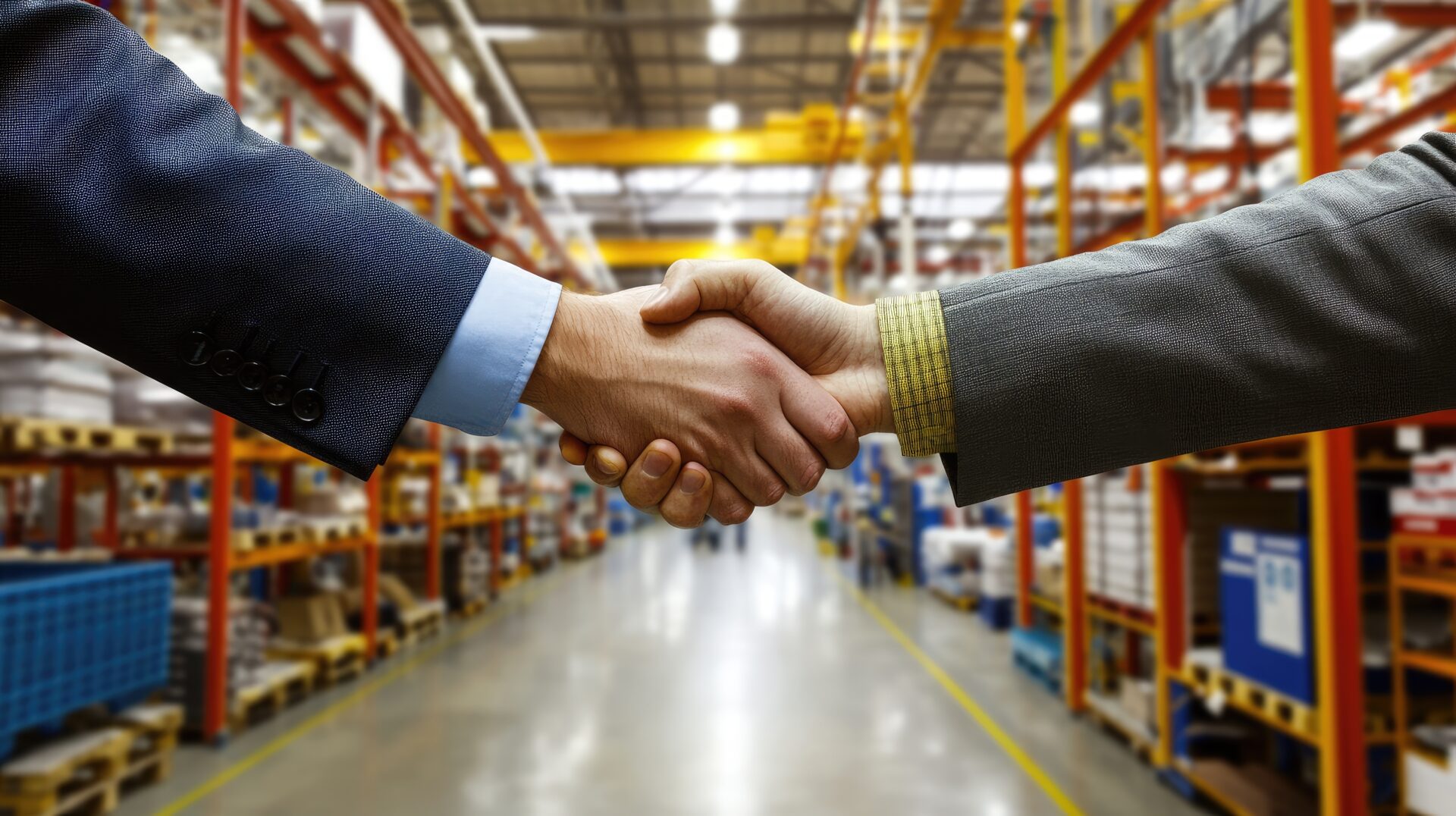
はじめに
この記事は、IATF 16949でサプライヤーマネジメントを進める中で、以下の関心をお持ちの方に向けて作られています。
- 新たに海外サプライヤーと取引を検討しているが、品質面や法令面で不安がある。監査や評価方法をどう進めればいいのか悩んでいる。
- サプライヤーにすぐIATF 16949を求めても実行が難しい場合、どのように対応すればよいのか知りたい。
- リコールや納期遅延を未然に防ぐため、サプライチェーンの管理を強化したいが、どんなポイントを押さえればいいのかわからない。
もし、ひとつでも当てはまるお悩みがあれば、それは決して珍しいことではありません。
自動車産業向け品質マネジメントシステム規格であるIATF 16949。その中でも、サプライチェーンをどこまで管理すればいいのか? というお悩みを抱えている方は多いのではないでしょうか。
この記事では、現役のIATF 16949審査員資格をもつ当社代表が、自動車産業向け品質マネジメントシステム規格であるIATF 16949の中でも、サプライヤーマネジメントに焦点を当てて解説します。段階的な品質マネジメントシステム開発の考え方や、具体的な評価方法、リスク事例などを交えながら、サプライヤーマネジメントをどのように強化すればよいかをわかりやすくまとめました。サプライヤーとの契約・監視・評価の各ステップを理解し、自社だけでなくサプライチェーン全体のリスクを軽減し、品質とブランド価値を高めるためのヒントをお伝えしていきます。
お役立ち情報をお届けするまで」もぜひご覧ください。
記事作成のポリシーや工程については、「先に内容をまとめると以下となります。
- サプライチェーン全体を管理する重要性
- 外部提供部品・プロセスの品質や納期リスクが、最終製品の品質と顧客満足度を左右します。
- 「リコール」「納期遅延」「コンプライアンス違反」を避けるため、サプライヤーの管理をしっかりと運用しましょう。
- 5ステップで理解する
- 要求事項の検討と方針策定→サプライヤーの選定→要求事項の伝達→リスクに応じた管理→監視・開発・改善
- これらを順序立てて進めることで、サプライヤーマネジメントの抜け漏れを防止できます。
- サプライヤー評価・選定・監視の具体的ポイント
- 品質・納入パフォーマンス
- リスク評価
- 品質マネジメントシステムの適合レベル
- リスクベースアプローチと段階的品質マネジメントシステム開発
- ISO 9001認証から始め、最終的にはIATF 16949へ段階的にステップアップ。
- 顧客要件や自社独自のリスク評価を合わせ、継続的にPDCAを回す。
- 認証取得以上の価値を得るには
- 品質マネジメント体制のレベルアップすることは、ブランド力向上や新規ビジネス獲得の機会にもつながります。
- 当社ではコンサルティング/トレーニング/内部監査サービスを通じ、単なる認証取得に留まらない「競争優位の確立」をサポートしています。
当社の詳細については、「会社概要」でご紹介しておりますので、ご興味があれば併せてご覧ください。
では、詳しく見ていきましょう。
IATF 16949とサプライヤーマネジメント:なぜ重要なのか
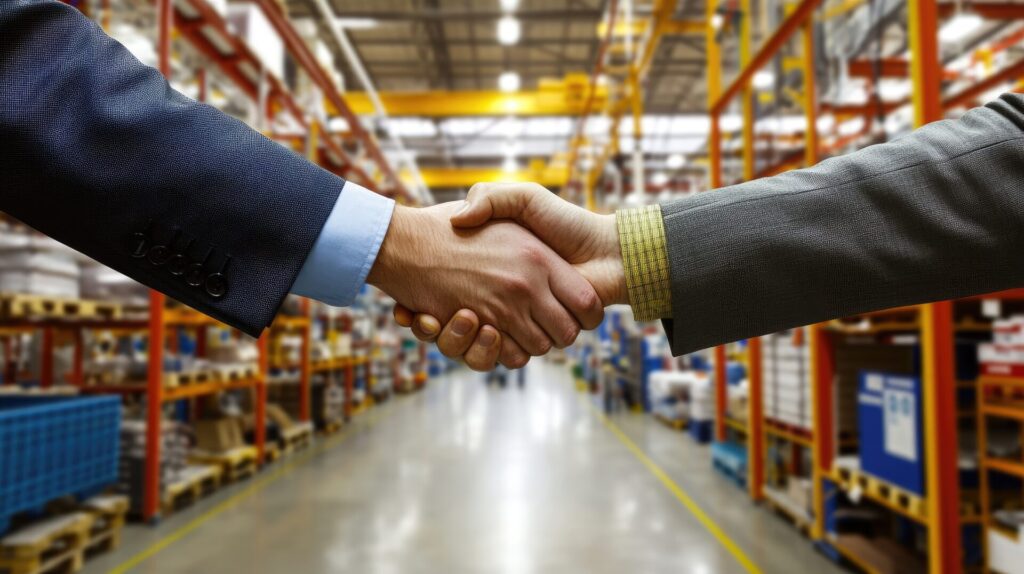
自動車産業向け品質マネジメントシステムであるIATF 16949は、サプライチェーン全体の品質を底上げし、最終的に顧客満足度を向上させることを目的としています。自社内のプロセスのみならず、外部から提供される部品・材料・サービスの品質・納期・リスク管理も含めて総合的にマネジメントすることが不可欠です。
サプライヤーマネジメントが重要な理由
- 部品品質が完成品の品質を左右
自動車部品は多段階のサプライチェーンを経由して組み上げられます。重要部品や特殊工法を外部に委託している場合、サプライヤーの品質管理レベルが直結して最終製品の品質に影響します。 - 納期・コスト面でのリスクヘッジ
サプライヤーの品質不具合や納期遅延は、自社製品の納期遅延・コスト超過を招く大きなリスクです。IATF 16949はこのリスクを低減するための管理手法を明確化しています。 - 顧客及び法規制要求事項への適合
自動車業界は、安全性や環境対応の面で厳格な法令・規制をクリアする必要があります。サプライヤーを含めてトータルでコンプライアンスを遵守することが求められます。
当社は「品質を競争優位のコアに据える」という基本姿勢を大切にしています。サプライヤーマネジメントを強化することで、自社だけでなくサプライチェーン全体のリスクを軽減し、品質とブランド価値を高めることが可能になります。
IATF 16949の要求事項を理解する
実際の業務では「サプライヤーを選定し、契約し、監視し、発展させる」といった流れで取り組むのが一般的です。ここでは、この流れを5つのステップに分けてご紹介します。
- 要求事項の整理
- まずは、自社と顧客、そして法令・規制の要件を明確にし、どのようなプロセス・製品・サービスを外部提供者から調達するのかを整理します。
- 手直し、校正サービスなど、顧客要求事項に影響する可能性があるものはすべて対象に含める点が重要です。
- 基本方針の策定
- サプライヤーマネジメントで何を重視するのか(品質最優先、リスク低減、コストバランスなど)を社内方針として定め、部門間で認識を共有します。
- サプライヤーに求める品質水準や納期遵守率の目標値も、この段階で大まかに設定しておくとスムーズです。
- サプライヤー評価・リスク分析
- 新規サプライヤーを選ぶ際は、品質実績(不良率や顧客クレームなど)・納期遵守率・財務状況・事業継続計画といった多角的な視点から評価を行います。
- IATF 16949では、サプライヤーの品質マネジメントシステムの成熟度をチェックすることも要求されています(ISO 9001やIATF 16949認証の有無など)。
- リスク分析により、供給停止や重大不具合が発生した場合の影響度と可能性を評価し、選定基準を文書化します。
- 複数部門を巻き込んだ意思決定
- 品質部門だけでなく、調達・生産技術・財務など部門横断的に評価を行うことで、より客観的かつ現実的な選定が可能になります。
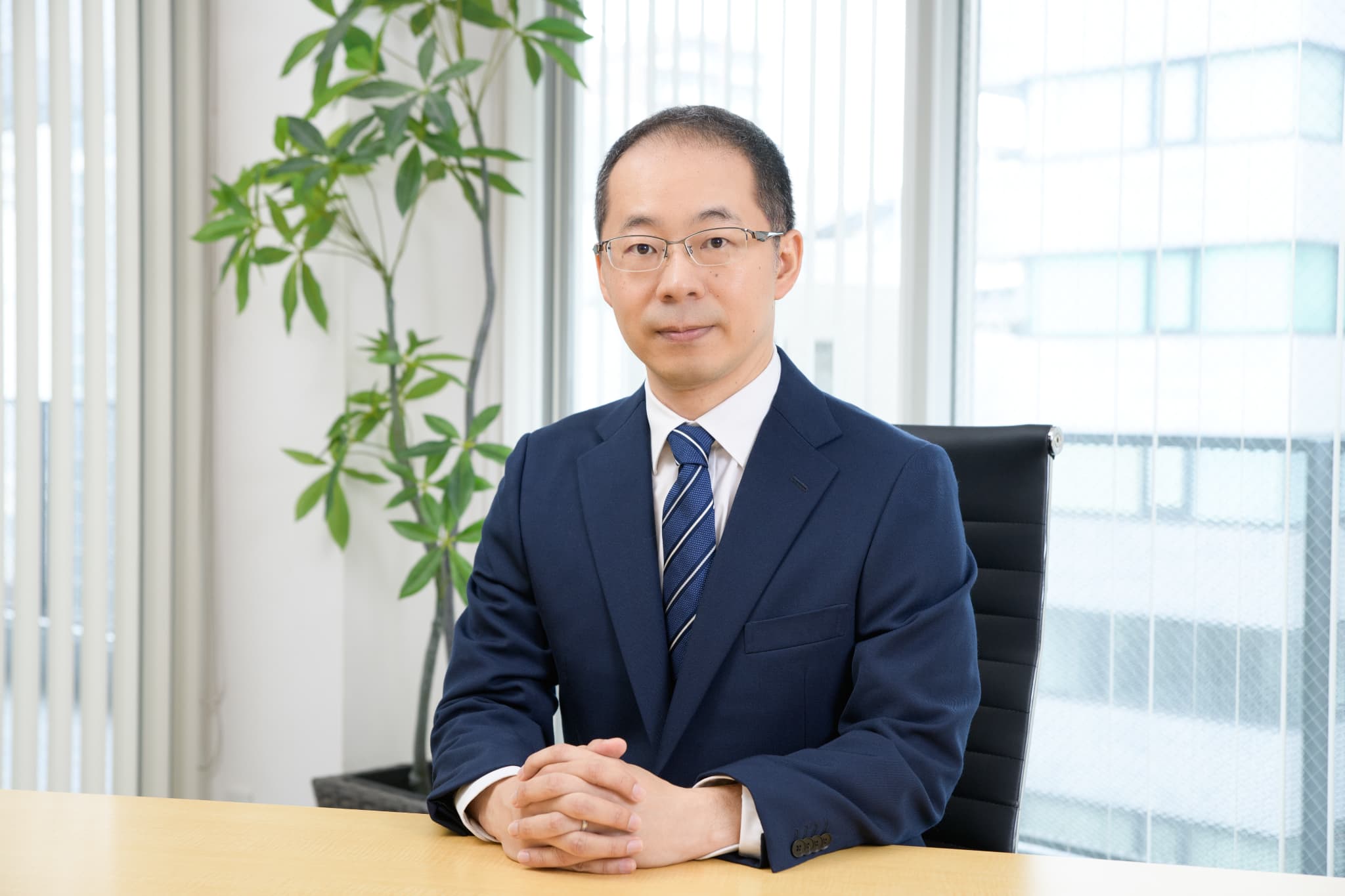
コスト削減を優先して海外サプライヤーと契約した結果、品質不良が発生し、その対応で苦労した事例がありました。リスク評価の不足は大きなコストと損害をもたらすことがあります。
- 契約条件の明確化
- 選定後に具体的な契約を結ぶ際、品質管理要求や特殊特性(安全部品など)管理を含め、要求事項を明確に伝達します。
- 顧客要求、法令・規制要求、仕向け地の要件(輸出入規制など)についても、サプライヤーと認識を一致させることが重要です。
- サプライチェーン全体への周知
- 必要に応じて、サプライチェーンのさらに下流(2次・3次サプライヤー)にも要求事項が的確に展開されるよう、情報伝達ルートを確立します。
- 管理レベルの決定
- リスクが高い部品・プロセスについては受入検査や第二者監査などの厳格な管理を行い、リスクが低い場合は管理を一部簡略化するなど、拡大・縮小の判断基準をあらかじめ定めます。
- 重要部品のアウトソーシングは、“自社がコントロールすべきプロセス”であるという認識を強くもつことが重要です。
- 法令・規制要求事項への適合
- 環境規制や安全規制など、自動車産業特有の厳しい要求を満たすためには、仕向け先の法規制にも注意が必要です。
- たとえば、化学物質関連の規制(REACH、RoHSなど)への適合確認、輸出入制限の把握なども、この段階で管理方法を決めておきます。
- 継続的な監視とパフォーマンス評価
- 定期的に品質指標(不良率、クレーム件数、納期遵守率など)をモニタリングし、必要に応じて是正・予防処置を要求します。
- 第二者監査(サプライヤー監査)を計画的に実施し、サプライヤーの品質マネジメントシステムの実態を把握・改善するプロセスが重要。
- 監査結果や評価データは文書化し、サプライヤーと共有することで、次のステップへのインプットにします。
- サプライヤーの品質マネジメントシステム開発
- IATF 16949では、サプライヤーに対して段階的にIATF 16949認証を目指す品質マネジメントシステム開発を推奨するよう求めています。
- 当初はISO 9001認証からスタートし、最終的にIATF 16949を取得していくロードマップも有効です。
- サプライヤーの改善プログラム
- 重大な不具合があった場合や、業績が不安定なサプライヤーには、改善計画を要求し、進捗を定期的にフォローアップ。
- 企業規模が小さいサプライヤーでもスムーズに導入できるよう、段階的なサポートを行うと、供給停止など大きなリスクを回避しやすくなります。
サプライヤー評価・選定・監視における具体的なポイント
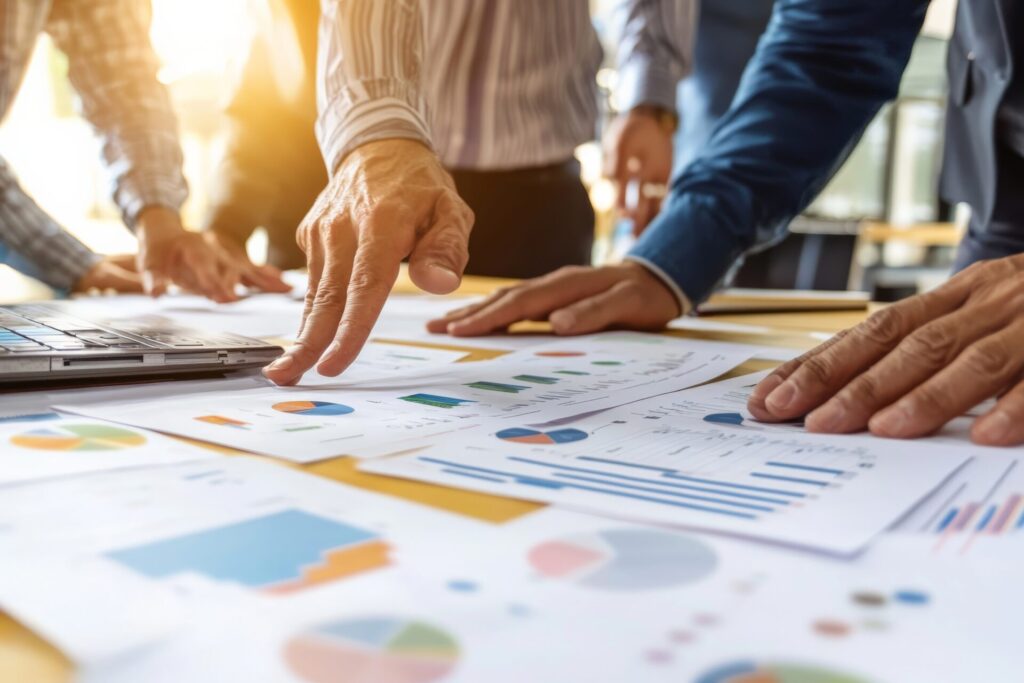
サプライヤー評価の基準づくり
- 品質パフォーマンス:不良率、クレーム件数、是正処置の迅速度など
- 納入パフォーマンス:納期遵守率や緊急時の対応力
- リスク評価:財務状況、自然災害リスク、法的リスクなど
- 品質マネジメントシステムの適合度:ISO9001、IATF16949認証状況、監査結果
「必要に応じた段階的開発」の取り入れ
IATF 16949では、製品品質に影響を与えるサプライヤーに対して最終的にIATF 16949認証に至るような品質マネジメントシステム開発を求める必要があります。しかし、すべてのサプライヤーがいきなりIATF 16949に対応できるわけではありません。そのため、まずはISO 9001認証による適合など、段階を踏んで品質マネジメントシステムを成熟させるアプローチが有効です。
選定プロセスとモニタリング
- 初期選定:審査や監査を組み合わせて、サプライヤーの適格性を検証。
- 継続監視:定期的な評価指標(PPM、不具合件数など)をモニタリングし、必要に応じて改善指導や第二者監査を実施。
- 再評価:重大な不具合・品質トラブルがあった場合、サプライヤーとしての適格性を再検証し、改善計画をフォローアップ。
第二者監査の有効活用
- 高リスクのサプライヤーや品質マネジメントシステムの成熟度が低いサプライヤーには第二者監査の実施がおすすめです。
- 監査報告書や評価結果を文書化し、社内共有することで改善アクションを明確化・追跡できます。
- 「自動車プロセスアプローチ」の考え方と整合性をとることも重要です。
リスクアプローチとサプライヤーの品質マネジメントシステム開発:長期的な競争優位を目指す
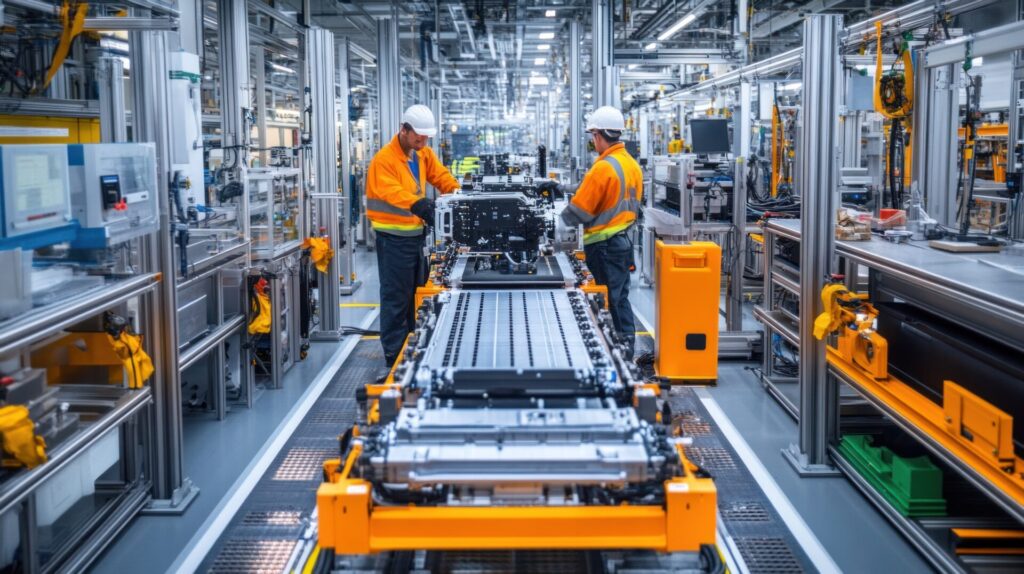
リスクベースアプローチの必要性
IATF 16949はISO 9001の枠組みをベースにしていますが、自動車産業固有のリスクに対応するため、より厳格なリスクアセスメントを求めています。サプライヤーマネジメントにおいても、財務面・品質面・納期面・コンプライアンス面といったリスクを多面的に評価し、コントロールする仕組みが不可欠です。
サプライヤー品質マネジメントシステム開発と段階的アプローチ
- ISO 9001認証の取得から始めて、最終的にIATF 16949に対応できるよう段階を踏む
- サプライヤーの現状パフォーマンスをデータで可視化し、PDCAサイクルを回す
継続的改善の仕組み
- サプライヤーとの定期的なコミュニケーション(レビュー会議やオンラインミーティングなど)
- 品質目標の共有と不具合時の報告フローや責任分担
- 「品質保証」を経営戦略に組み込むことで、長期的な企業価値・ブランド力の向上にもつなげる
次のステージへ – 認証取得以上の価値を生み出すには
IATF 16949は単なる「認証取得」や「お客様からの要求に対応する」だけではなく、自社の競争優位を築く絶好の機会になります。
- 高度な品質管理体制を整えることは、市場からの信頼獲得につながり、結果として新規ビジネスの拡大やブランド価値向上にも寄与します。
- 当社では、審査員としての視点+認証機関責任者としてのマネジメント経験を掛け合わせ、単なる手順や書類づくりだけで終わらない「経営戦略としての品質保証体制づくり」を支援しています。
当社が提供する総合サポート
- コンサルティングサービス: IATF 16949 / JIS Q 9100に精通した専門家が、認証取得からシステム構築まで支援。現場に負荷をかけずに運用できる仕組みをご提案します。
- トレーニングサービス: 自動車・航空機産業に特化した包括的な人材開発プログラム。短期的な認証対策から長期的な組織変革まで一貫してサポートします。
- 内部監査サービス: 現役のIATF審査員が内部監査を代行し、リスクを早期発見&改善提案。負荷を軽減しつつ認証維持の精度を高め、自社の品質競争力を向上させます。
- サプライヤーマネジメントサービス: IATF 16949 / JIS Q 9100のノウハウを活かし、サプライヤー監査や改善活動を総合的にサポート。品質不正リスクを早期に発見し、継続的な改善策を浸透させることで、サプライチェーン全体の品質とブランド価値を高めます。
当社の詳細については、「会社概要」からご覧いただけます。
「まずは無料で話を聞いてみたい」「認証取得のイメージを具体化したい」という方は、ぜひ初回30分の無料相談をご利用ください。
まとめ
ここまで、IATF 16949でのサプライヤーマネジメント強化に向けたポイントを解説してきました。
- サプライチェーン全体を管理する重要性
- 外部提供部品・プロセスの品質や納期リスクが、最終製品の品質と顧客満足度を左右します。
- 「リコール」「納期遅延」「コンプライアンス違反」を避けるため、IATF 16949の管理をしっかりと運用しましょう。
- 5ステップで理解する
- 要求事項の検討と方針策定→サプライヤーの選定→要求事項の伝達→リスクに応じた管理→監視・開発・改善
- これらを順序立てて進めることで、サプライヤーマネジメントの抜け漏れを防止できます。
- サプライヤー評価・選定・監視の具体的ポイント
- 品質・納入パフォーマンス
- リスク評価
- 品質マネジメントシステムの適合レベル
- リスクベースアプローチと段階的品質マネジメントシステム開発
- ISO 9001認証から始め、最終的にはIATF 16949へ段階的にステップアップ。
- 顧客要件や自社独自のリスク評価を合わせ、継続的にPDCAを回す。
- 認証取得以上の価値を得るには
- 品質マネジメント体制のレベルアップすることは、ブランド力向上や新規ビジネス獲得の機会にもつながります。
- 当社ではコンサルティング/トレーニング/内部監査サービスを通じ、単なる認証取得に留まらない「競争優位の確立」をサポートしています。
この記事を参考に、サプライヤーマネジメントの抜け漏れを見直し、サプライチェーン全体で品質とリスクをコントロールする体制づくりを進めてみてください。
IATF 16949でお悩みではありませんか?
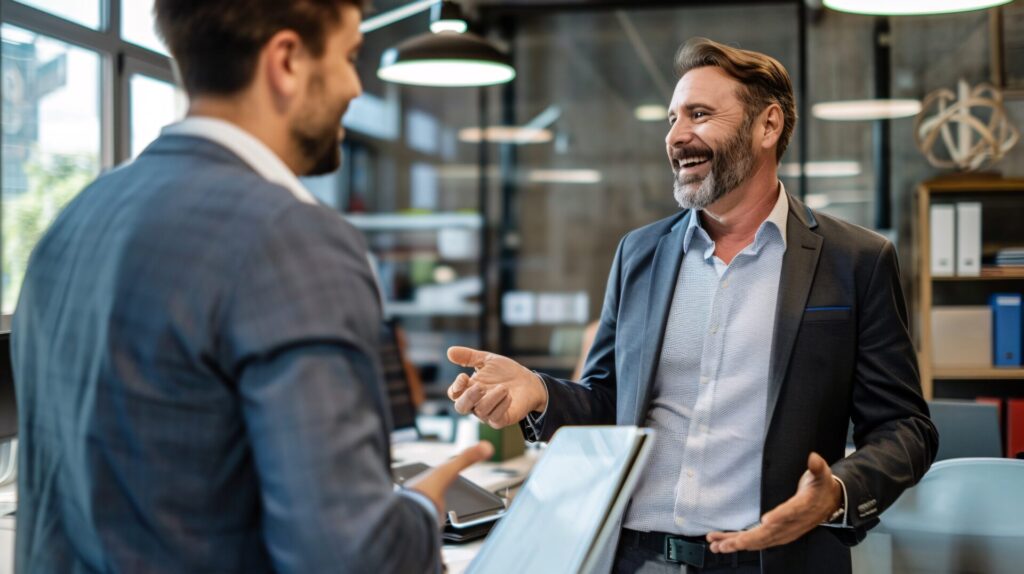
当社では、「認証取得」だけでなく、売上アップ・リスク低減・ブランド強化まで見据えたコンサルティングサービスやサプライヤーマネジメントサービスを提供しています。顧客要求が厳しい自動車や航空機産業で数多くの経験に基づき、現場で負担なく運用できる仕組みづくりを徹底的にサポートいたします。
もし、「うちの現場にも当てはめたいけれど、具体的に何から着手すれば…?」とお悩みでしたら、ぜひ初回30分の無料相談をご利用ください。
当社の詳細については、「会社概要」からご覧いただけます。
さらに学びたい方へ
FMEAのポイントを押さえて、
品質リスクを
事前に防ぎませんか?
効果的なFMEAの作り方や
運用ノウハウをわかりやすく
解説しています。
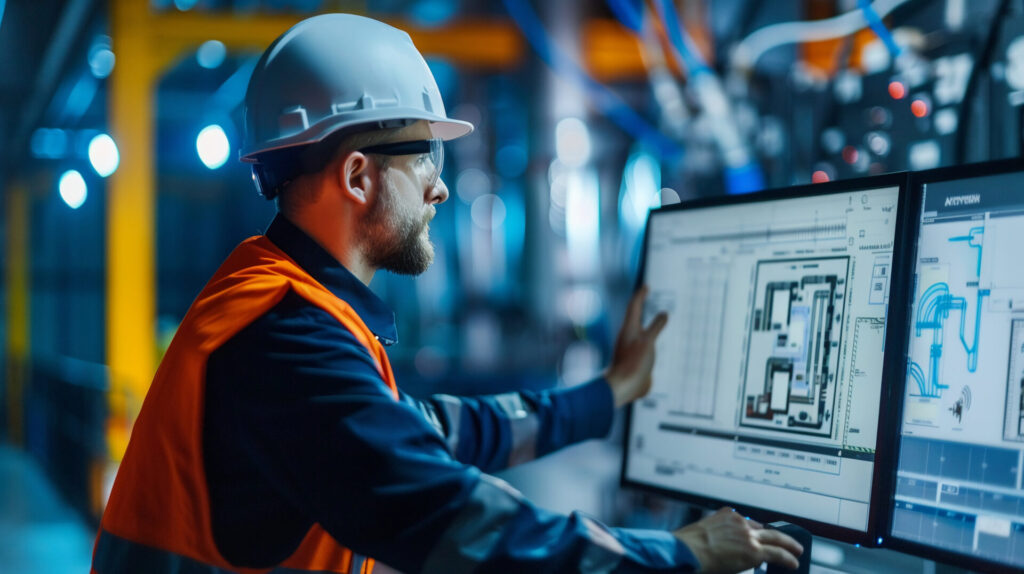
APQPの各フェーズを深く理解し、プロジェクト管理の精度を
高めませんか?
新製品立ち上げを
円滑に進める具体的な手法を、
初心者もわかりやすく学べます。
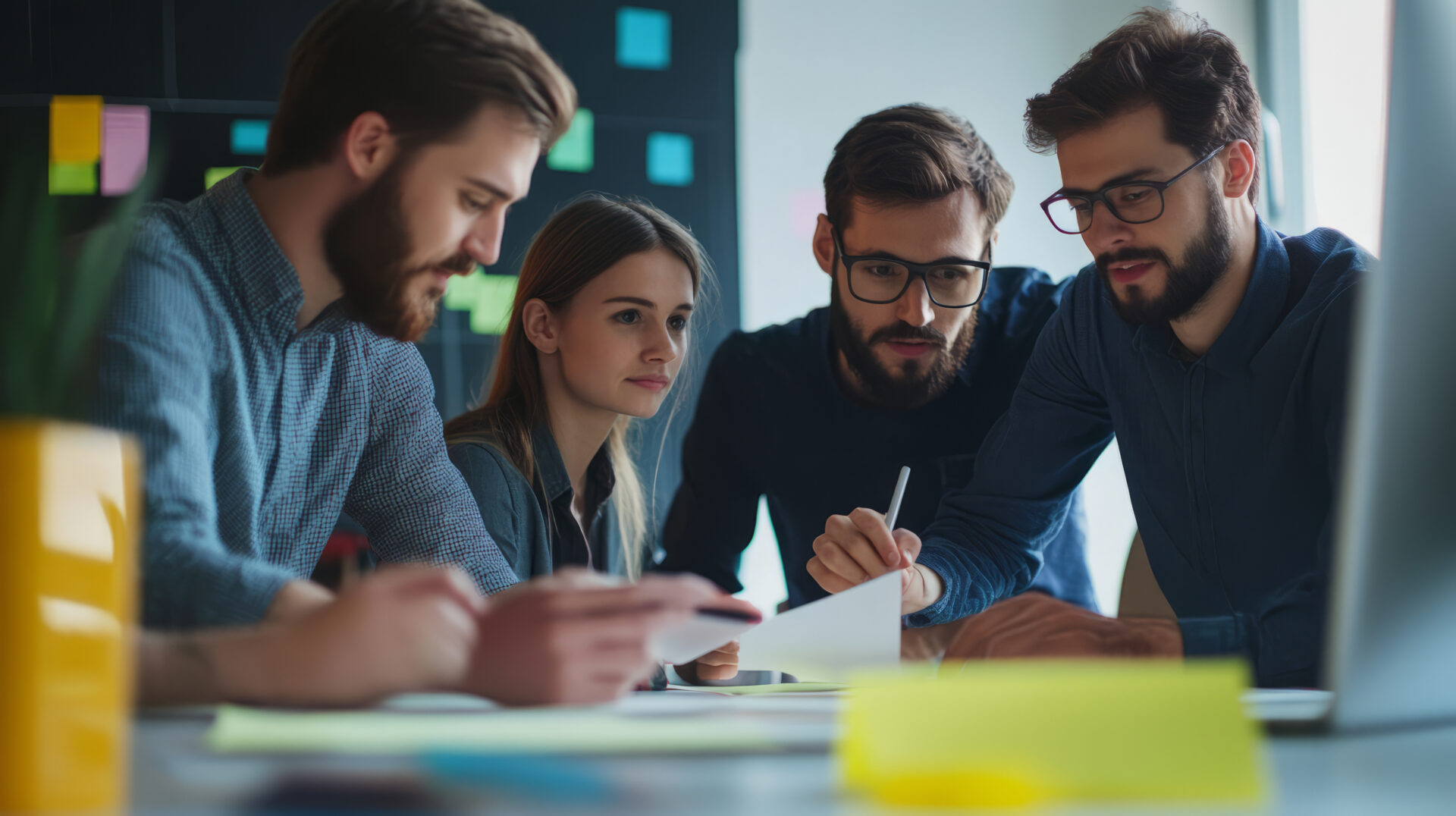
顧客からスムーズに承認されるコントロールプランの書き方を学びませんか?
実運用を踏まえて、コントロールプランの作成ポイントをわかりやすく解説しています。
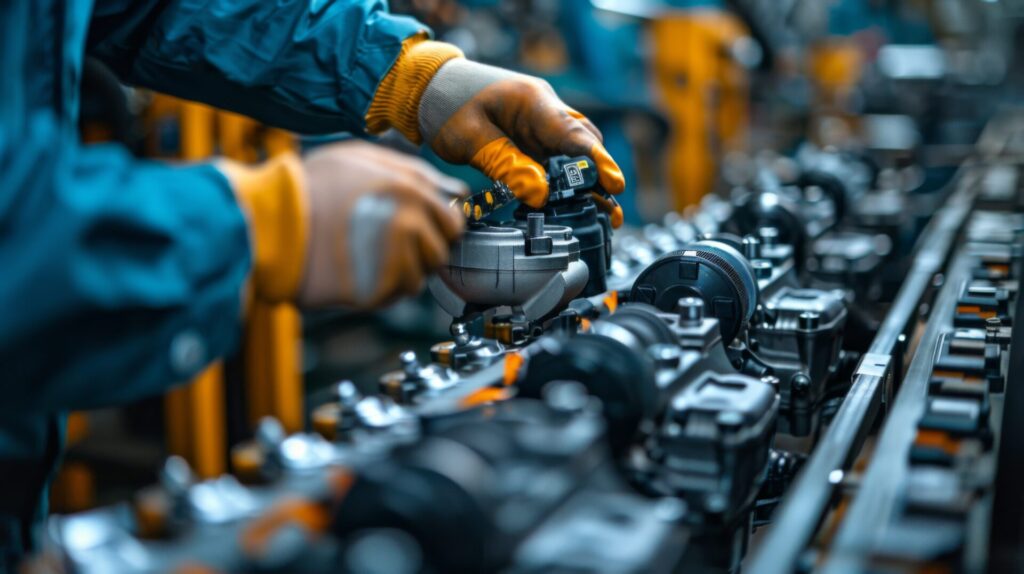
IATF 16949やJIS Q 9100に関する【お役立ち情報】を、他にも多数ご用意しています。
わかりやすい解説や、役立つノウハウを多数掲載していますので、ぜひ以下のページもご覧ください。
お役立ち情報一覧」を見る