IATF 16949のFMEAとは? – 不良品を減らす最大の機会を見逃すな
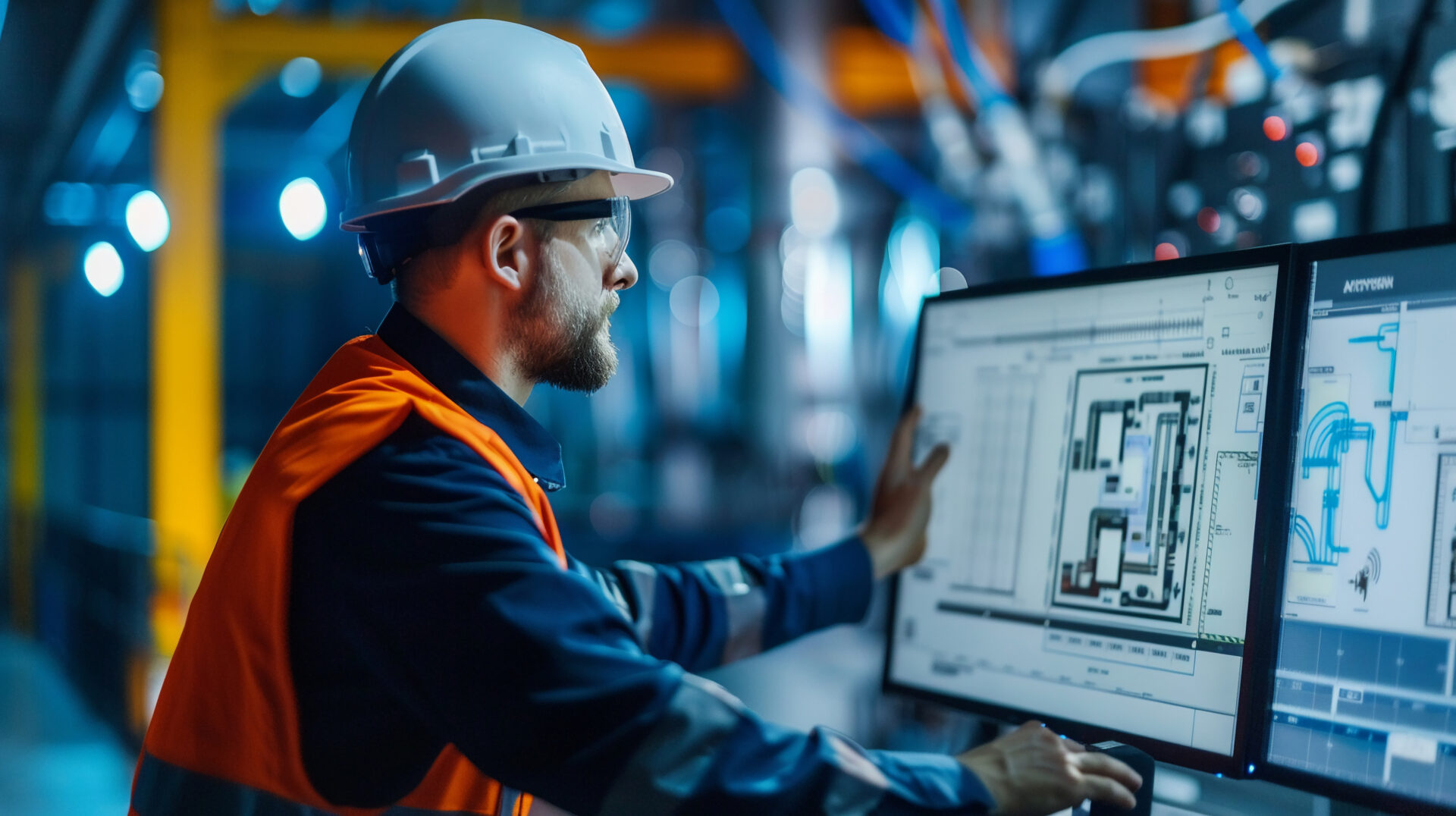
はじめに
この記事は、IATF 16949のFMEAを行う中で、以下の関心をお持ちの方に向けて作られています。
- FMEAのやり方はなんとなく知っているけど、本当に合っているのか自信がない…
- 進めてみたものの、重要なリスクを見落としていないか、不安で落ち着かない…
- 自身の経験が浅いせいもあって、FMEAのレビューで何をどう話せばいいか分からない…
もしこうした悩みをお持ちでしたら、それは珍しくありません。私も同じような経験をしてきましたが、不安や悩みをかかえながら長期間に渡り検討とレビューを重ね、何とか製品や工程の故障リスクを軽減させようと努力されている方は多いと思います。あなたも同じような悩みを抱えていませんか?
そこで、現役のIATF 16949審査員資格を有する当社代表が専門家としての経験から、IATF 16949で要求されているFMEAの基本を確認した上で、より効果的にFMEAを活用して不良リスクを減らすポイントについてわかりやすく解説します。
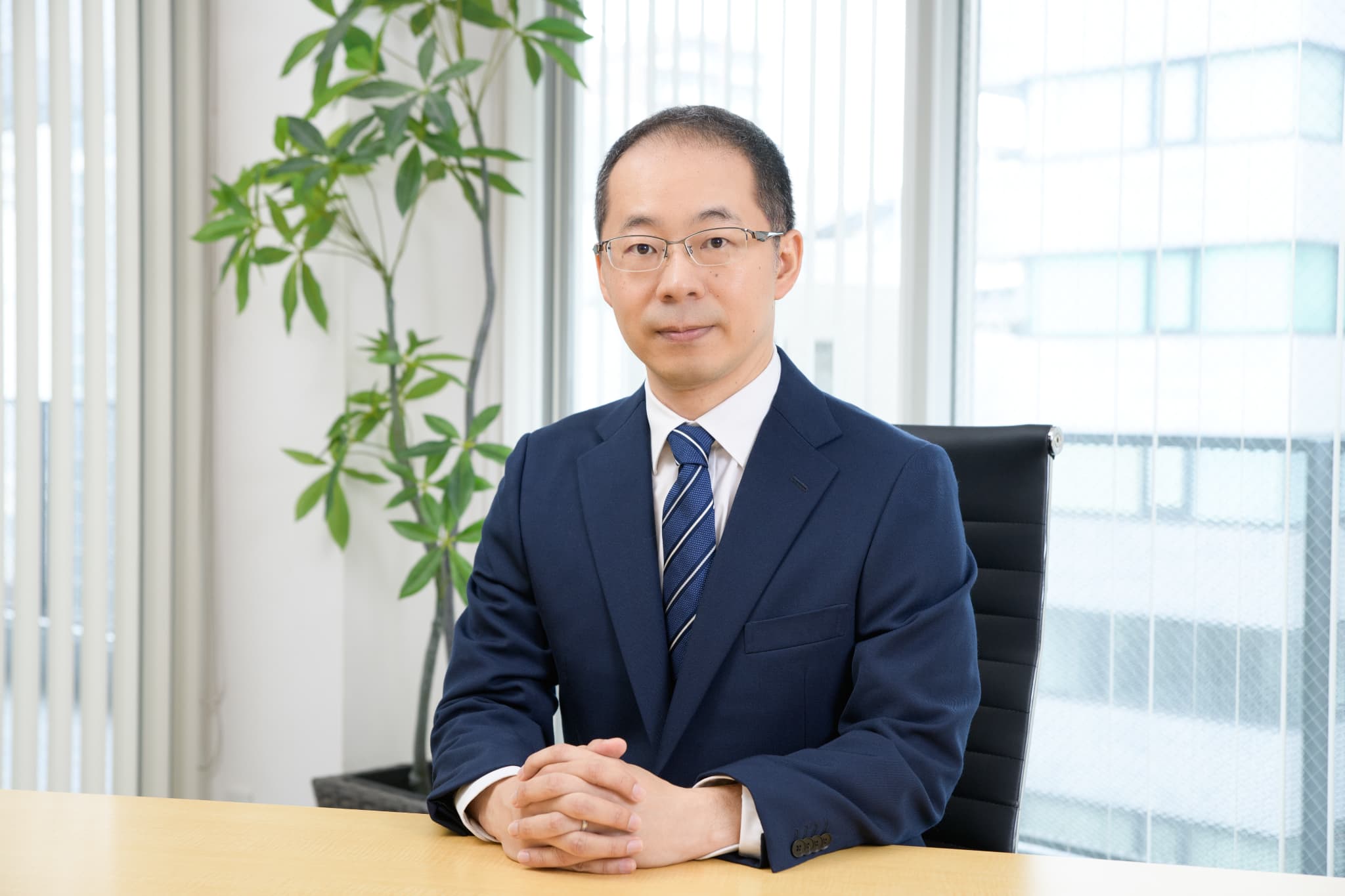
FMEAは“単なるチェックシート”ではなく、ビジネス成長のための強力な武器になります。これまで、数多くの企業を拝見させていただきましたが、FMEAの完成度が高い会社は結果として“ブランド評価”や“取引拡大”につながりやすいと感じています。
お役立ち情報をお届けするまで」もぜひご覧ください。
記事作成のポリシーや工程については、「先にまとめると以下となります。
- FMEAとは
FMEA(故障モード影響解析)は、製品や工程の潜在的な故障モードやその影響を体系的に評価し、リスクを事前に特定して予防的な処置を講じるための解析手法です。 - 実施ステップ
FMEAは主に以下の6つのステップで進められます。- 故障モードの特定
製品や工程を詳細に分解し、潜在的な故障モードを体系的に洗い出します。 - 影響の評価
故障モードが発生した場合の影響度(Severity)を評価します。 - 原因の特定
故障モードの原因を詳細かつ具体的に特定します。 - 発生頻度と検出度の評価
故障モードの発生頻度(Occurrence)と検出度(Detection)を評価し、リスク優先度(RPN)を算出します。 - リスク軽減に向けた処置の検討と実施
高リスクの故障モードに対して具体的な処置を計画・実施します。 - 処置の評価
実施した処置の効果を評価し、必要に応じて追加対策を講じます。
- 故障モードの特定
- FMEAの効果を上げるために
設計や技術部門だけでなく、他の部門もインタフェース情報を明確にするよう支援しましょう。過去の不良データや市場データを分析し提供したり、部門横断チームでレビューを行うことで、FMEAの精度と効果を高めることができます。 - 継続的な改善
FMEAは一度実施して終わりではなく、製品や工程のライフサイクル全体を通じて継続的に改善を図ることが重要です。
当社の詳細については、「会社概要」でご紹介しておりますので、ご興味があれば併せてご覧ください。
では、ここから詳しく見ていきましょう。
FMEAの基礎
FMEAとは?
FMEA (Failure Mode and Effects Analysis:故障モード影響解析)のことで、製品や工程の潜在的故障モードや原因を体系的に評価して、リスクを事前に特定して予防的な処置を講じるための解析手法です。そのため、リスクマネジメントの強力なツールとなります。
主に設計段階で実施される活動です。潜在的故障の特定、その影響度(厳しさ)・発生頻度・検出度を基準に基づいて評価します。
FMEAは以下の2種類あります。
- DFMEA(Design FMEA):製品に対するもので、製品設計段階での故障リスクを評価
- PFMEA(Process FMEA):製造工程(プロセス)に対するもので、製造工程での故障リスクを評価
特にIATF 16949では、製品設計・工程設計ともに「リスクを先回りして洗い出し、リスクを低減する」ことが求められます。
自動車・航空機産業では安全性・信頼性への要求が非常に高いため、FMEAが不良予防と顧客満足度向上の鍵となります。
IATF 16949のFMEAの目的は?
IATF 16949では、設計活動や工程設計のアウトプットとしてFMEAの実施が要求されています。
その主な目的は、
- 製品や工程のリスクを事前に特定して軽減する
- 無駄なコストやクレームを未然に防ぎ、顧客への信頼を向上させる
- 競争優位のコアである“品質”を高め、ビジネス成長やブランド強化につなげる
という点にあります。特に自動車・航空機産業での厳しい要求を満たすためには、先回りのリスク管理が不可欠です。
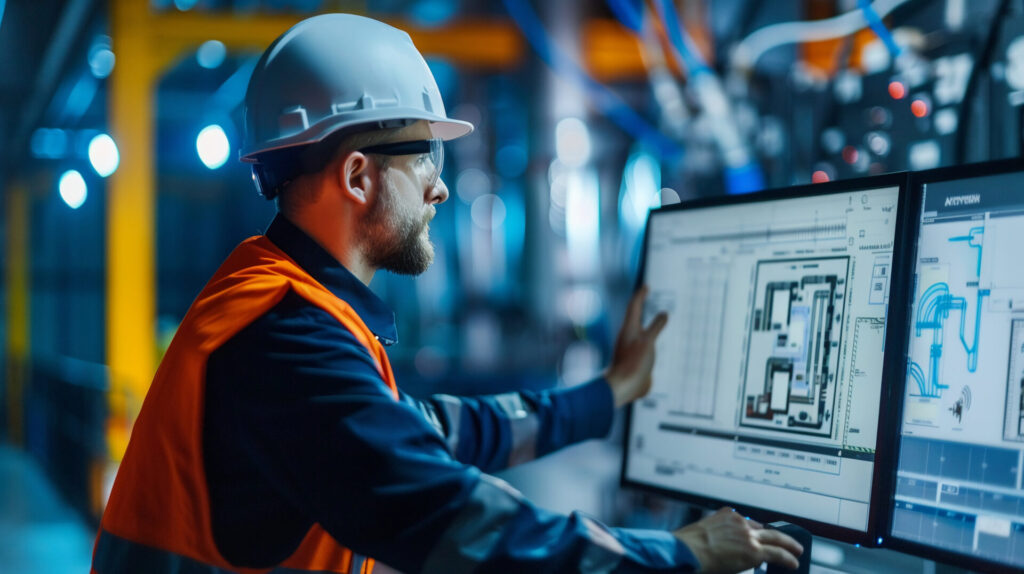
いつ実施するの?
IATF 16949では設計活動のアウトプットとして要求されています。JIS Q 9100では同じ単語は明示的に使われていないものの、運用リスクマネジメントとして同等のことが要求されています。
主に製品設計や工程設計段階で実施される活動となります。その他にも、是正処置プロセスで処置を検討するとき、製品や製造工程を変更する際にも利用されます。継続的に見直し、ライフサイクル全体を通じて改善していくのが理想です。
IATF 16949,JIS Q 9100の詳細については、以下の記事をご確認ください。
FMEAを具体的に実施する6つのステップ
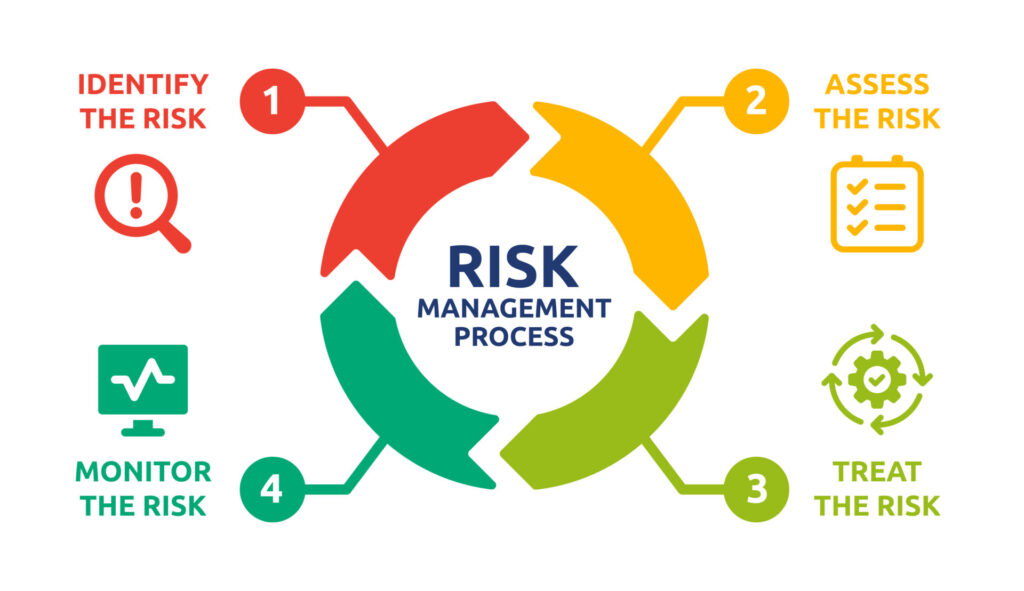
ここからは、FMEAを進めるうえで押さえておきたい6ステップをご紹介します。
FMEAの最初のステップは、分析対象である製品や製造工程を各構成要素や機能毎に詳細に分解し、想定できる潜在的な故障モードを体系的に洗い出していきます。
ポイント
- 過去の不良事例や市場不具合のリストアップ
過去に発生した不良事例や市場クレーム、先行開発や他製品のデータを整理しておくことで、故障モードの洗い出しが容易になります。これにより、実際に問題が発生しやすい箇所やパターンを事前に把握し、分析の精度を高めることができます。
故障モードが実際に発生した場合の製品や工程に与える影響(Severity)を詳細に評価します。その影響ランクを予め定めた評価基準で数値化し評価します。
厳しさ(Severity)
- 定義
厳しさとは、ある故障モードが与える最も重大な製品や工程への影響の程度のことです。 - 評価尺度
製品設計:厳しさは「車両の安全な操作に影響を与える」「主要機能の喪失または低下」「二次機能(快適性や利便性)に関する機能の喪失または低下」「外観不良や騒音の不快」などの基準で10段階でランク付けします。
工程設計:厳しさは「作業者を危険にさらす」「生産ラインの操業停止」「生産ラインのタクト低下」「生産品の手直しが必要」「わずかなエラーが発生」などの評価基準で10段階にランク付けします。
ポイント
- 具体的な評価基準の設定:影響度ランクを具体的に予め定義し、全員が共通の基準で評価できるようにします。
- 客観的データの活用:ユーザーインタビューや市場データ、過去の不良データを基に、影響度を客観的に評価します。
- 継続的な見直し:製品や市場の変化に応じて、影響度の評価基準やスコアを定期的に見直します。
FMEAの第三ステップでは、特定された故障モードに対する原因をできるだけ具体的かつ詳細ンに特定することが求められます。また、原因は一つだけでなく複数存在する可能性もあり、それぞれを漏らさず明確にする必要があります。細かく特定することで、効果的な処置方法を検討することが可能になります。さらに、原因は製品や工程の潜在的な弱点として捉え、根本的な改善に繋げていくことが重要です。
ポイント
- フィードバックループの確立
製造現場やサービス現場からのフィードバックを定期的に収集し、製品や工程の故障モードを把握し、特定された故障モードの原因に対して継続的な改善策を講じ、FMEAのプロセスを通じて製品および工程の信頼性を向上させます。 - 詳細かつ具体的な原因特定
多角的なアプローチと共に、原因は細かく特定して、対策の効果を最大化できるようにしていきます。曖昧な原因ではなく、具体的な要因を明確にすることが重要です。 - 製品・工程の弱点を特定する
製品設計レビューで製品や製造工程の潜在的な故障モードの原因を洗い出し、信頼性の改善へとつなげていきます。
FMEAの第四ステップでは、特定された原因に基づき、発生頻度と検出度を評価します。これにより、リスク優先度(RPN)の算出が可能となります。
発生頻度(Occurrence)
- 定義
発生頻度とは、現行もしくは計画している予防管理を適用した場合、ある故障モードの原因が発生する可能性のことです。 - 評価尺度
発生頻度は「非常に低い」「低い」「中程度」「高い」「非常に高い」などの評価基準で10段階にランク付けします。
検出度(Detection)
- 定義
検出度とは、現行もしくは計画している検出管理において、ある故障モードが検出できる可能性のことです。 - 評価尺度
検出度は「ほとんど不可能」「非常にかすか」「かすか」「非常に低い」「低い」「中程度」「比較的高い」「高い」「非常に高い」「ほぼ確実に検出」などの評価基準で10段階にランク付けします。
ポイント
- データドリブンな評価
類似の製品やプロセスから得られた実績データを基に、発生頻度と検出度のランクを決定します。具体的には、過去の不良データや市場データを分析し、客観的な根拠に基づいてランク付けを行います。 - 一貫性のある評価基準の設定
発生頻度と検出度の評価基準を事前に定め、全ての評価者が同じ基準に基づいて評価を行うようにします。これにより、評価の一貫性と客観性が確保されます。
評価された影響度、発生頻度、検出度を基に、処置が必要な故障モードを検討して、リスクを軽減するための具体的な処置を計画・実施します。
ポイント
- 優先順位の明確化
厳しさ(Severity)の高い故障モードを最優先で対策し、その後に発生頻度(Occurrence)の高い故障モードや検出度(Detection)の低い故障モードを検討することで、効率的にリスクを軽減します。 - 多層的な対策
厳しさ(Severity)、発生頻度(Occurrence)、検出度(Detection)の各要素に対して適切な対策を講じることで、総合的なリスク軽減が可能となります。 - データに基づくアプローチ
実績データや市場データを活用し、客観的な根拠に基づいた対策を計画・実施します。
FMEAの最後のステップでは、処置の結果を確認して、影響レベル、発生頻度、検出度はどのように変化したかを予め定めた基準で評価します。実施した対策が期待通りの効果を発揮しているかを確認し、必要に応じて追加対策を講じます。以下のポイントに基づいて、処置の評価プロセスを詳細に説明します。
ポイント
- 定めた基準に基づく客観的評価
処置の効果を定量的および定性的に評価し、基準に基づいてリスク軽減の達成度を判断します。 - 検証と再評価の重要性
対策が有効であることを検証し、必要に応じて追加の対策を講じることで、リスク管理の精度を高めます。 - 継続的なFMEAの見直しサイクル確率
FMEAは一度実施して終わりではなく、製品や工程のライフサイクル全体を通じて継続的に改善を図ります。
FMEAの効果を上げるために、お勧めしたいこと
FMEAは設計・技術部門が主担当ですが、他部門でも多くの貢献が可能です。
その中でも、FMEAの精度と効果を高めるために、お勧めしたいことを紹介します。
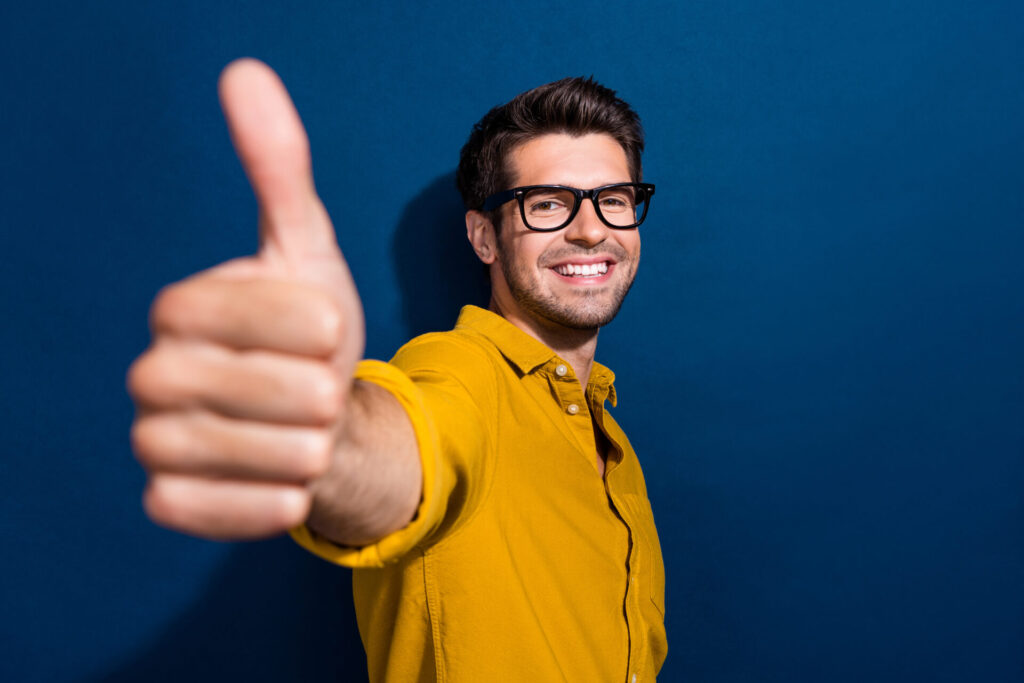
設計・技術部門に感謝と協力体制を
- 設計や技術担当者は高い専門性と優れた深い分析を提供してくれる存在です。まずは彼らの貢献に改めて感謝し、彼らを信じることで前向きで積極的なFMEAを進めましょう。
- プロジェクトのキックオフ、レビュー会議、雑談時に感謝の気持ちを伝えましょう。
インタフェース情報を明確にする支援
- FMEAにおいて分析すべき対象を正確に理解してもらうことが必要です。特に、インタフェースの部分に問題の多くが潜んでいることが経験則から知られており、インタフェースの取り扱いは大切です。
- 顧客や同僚に確認をするなど、ブロック図、パラメータ図、フロー図などを使って視覚的に各要素との情報や力学的な相互作用を明確化しましょう。
過去の不良データ、工程内の不良データ、市場データを分析して提供しよう
- 厳しさ・発生頻度・検出度のランクを決定する際の有用なインプットとなります。過去に発生した類似の問題に対処でき、発生する可能性のあるプロセス・条件、故障の影響について妥当な評価に結び付けることができます。
- FMEAを開始する前に過去の不良、クレーム、工程内不良、市場不具合に関するデータを収集・整理します。社内のデータベースシステムや品質記録から関連するデータを集めます。FMEAを始める前にデータ収集・分析をしておくと、客観的かつ説得力ある評価ができます。
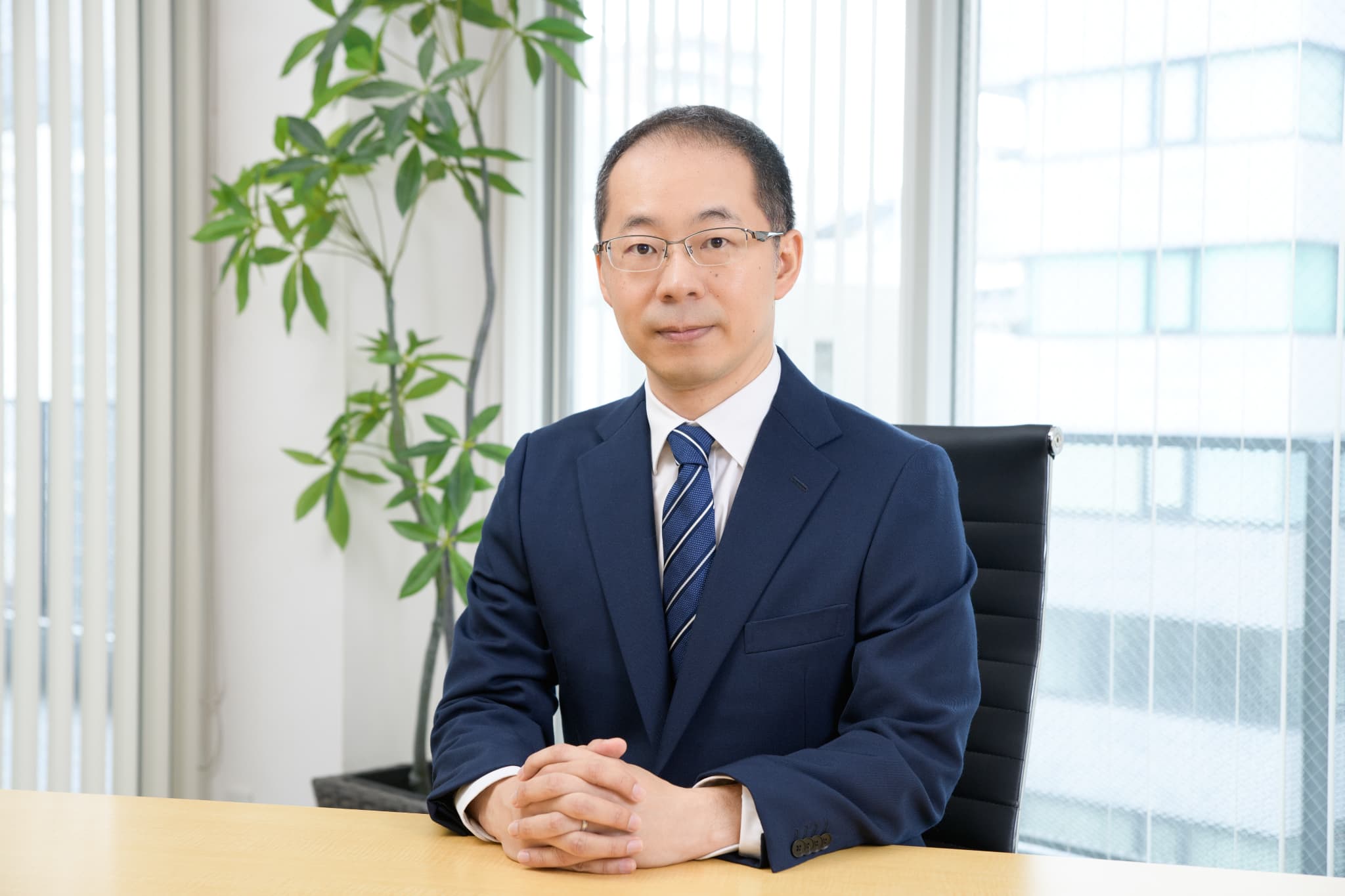
これらのデータは日頃から収集、整理しておくことが大切ですね。
部門横断チームでレビュー
- 正確で効果的な評価ができるように多様な視点を入れ込みます。一部門のみでリスク分析を行うと、リスク特定の漏れ(見落とし)や、リスクレベルが正しく評価されない心配があります。多様な部門の視点を取り入れることで、リスク特定の精度が向上します。
- デザインレビューで、FMEAに必要なインプットに漏れがないか、リスクレベルは基準に従って評価されているかを確認しましょう。
フォロー体制で確実な実施
- フォローしリスク軽減に向けた処置を確実に実施することで、はじめてFMEAの効果は得られます。逆にいうと、指摘されたリスクに対して実際に対策しなければ効果はゼロです。
- デザインレビューや審査会でリスクの軽減に向けた処置がすべて完了しているか、リスクレベルがまだ受け入れられていない未解決のものはないか確認しましょう。
さらに当社が提供できるサポート
当社は「お客様が自己実現とビジネス成長を達成し、自動車・航空機産業の新時代をリードできるように」という理念のもと、IATF 16949 / JIS Q 9100に特化した品質マネジメントシステムのコンサルティングを強みとしています。FMEAに関しても、下記のような形でサポートが可能です。
- コンサルティングサービス
- 認証機関の審査員・責任者としての経験を活かし、最適なFMEAの運用方法をアドバイスします。
- 「認証取得がゴールで終わらない」よう、品質をコアとした経営戦略との融合を提案します。
- 不良削減だけでなく、ブランド強化・リスク低減・売上向上を狙える包括的な支援が特徴です。
- トレーニングサービス
- IATF 16949 / JIS Q 9100の理解を深めるための講座をはじめ、現場に落とし込めるFMEAトレーニングも提供しています。
- 企業文化を大切にしながら、短期の成果(不良削減)と長期的な企業価値の向上(ブランド力・人材の成長)を両立します。
- 内部監査サービス
- FMEAや品質マネジメントシステムが実際に有効に回っているか、内部監査の視点から確認し、改善ポイントをアドバイスします。
- 審査員資格をもつ専門家が支援するため、外部審査対応も安心です。
- サプライヤーマネジメントサービス
- IATF 16949 / JIS Q 9100のノウハウを活かし、サプライヤー監査や改善活動を総合的にサポート。
- 品質不正リスクを早期に発見し、継続的な改善策を浸透させることで、サプライチェーン全体の品質とブランド価値を高めます。
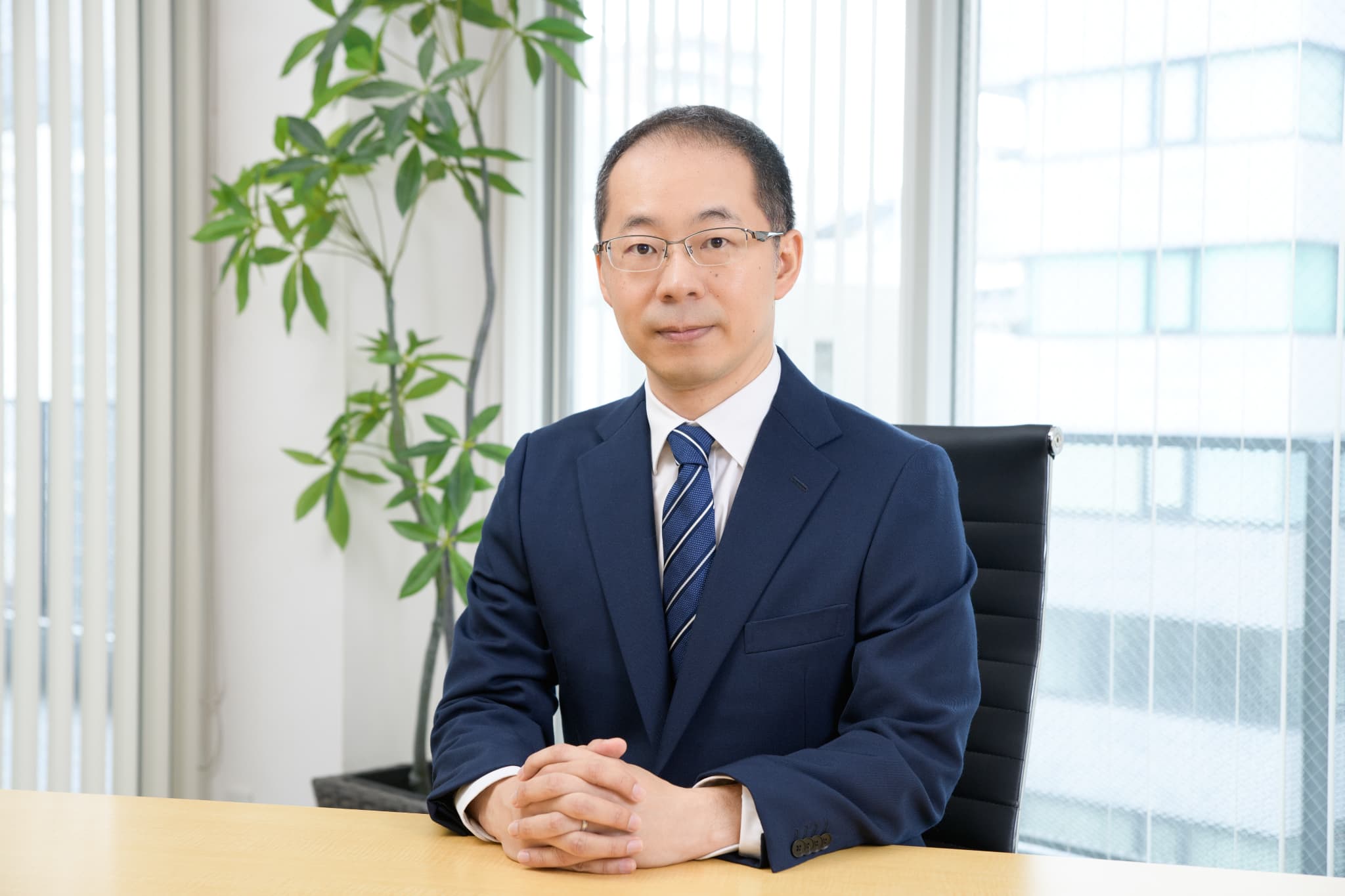
FMEAをしっかり運用している企業は、取引先や認証機関からも“品質管理が行き届いている”と高く評価されやすいです。品質は競争優位のコアになり、ビジネス拡大や新規事業創出にも大きく貢献します。当社は、自動車・航空機分野で培った豊富な知見をフル活用し、お客様のビジネス成長を全力でサポートします。
当社の詳細については、「会社概要」からご覧いただけます。
「まずは無料で話を聞いてみたい」「認証取得のイメージを具体化したい」という方は、ぜひ初回30分の無料相談をご利用ください。
まとめ
IATF 16949で要求されるFMEAの基本を確認し、FMEAを効果的に実施するためのポイントについて解説しました。
- FMEAとは
FMEA(故障モード影響解析)は、製品や工程の潜在的な故障モードやその影響を体系的に評価し、リスクを事前に特定して予防的な処置を講じるための解析手法です。 - 実施ステップ
FMEAは主に以下の6つのステップで進められます。- 故障モードの特定
製品や工程を詳細に分解し、潜在的な故障モードを体系的に洗い出します。 - 影響の評価
故障モードが発生した場合の影響度(Severity)を評価します。 - 原因の特定
故障モードの原因を詳細かつ具体的に特定します。 - 発生頻度と検出度の評価
故障モードの発生頻度(Occurrence)と検出度(Detection)を評価し、リスク優先度(RPN)を算出します。 - リスク軽減に向けた処置の検討と実施
高リスクの故障モードに対して具体的な処置を計画・実施します。 - 処置の評価
実施した処置の効果を評価し、必要に応じて追加対策を講じます。
- 故障モードの特定
- FMEAの効果を上げるために
設計や技術部門だけでなく、他の部門もインタフェース情報を明確にするよう支援しましょう。過去の不良データや市場データを分析し提供したり、部門横断チームでレビューを行うことで、FMEAの精度と効果を高めることができます。 - 継続的な改善
FMEAは一度実施して終わりではなく、製品や工程のライフサイクル全体を通じて継続的に改善を図ることが重要です。
FMEAを適切に活用することで、製品や工程の信頼性を向上させ、不良品の削減や顧客満足度の向上につなげることが可能です。ぜひ、FMEAを最大限に活用し、品質管理の向上に役立ててください。
FMEAやIATF 16949でお悩みではありませんか?
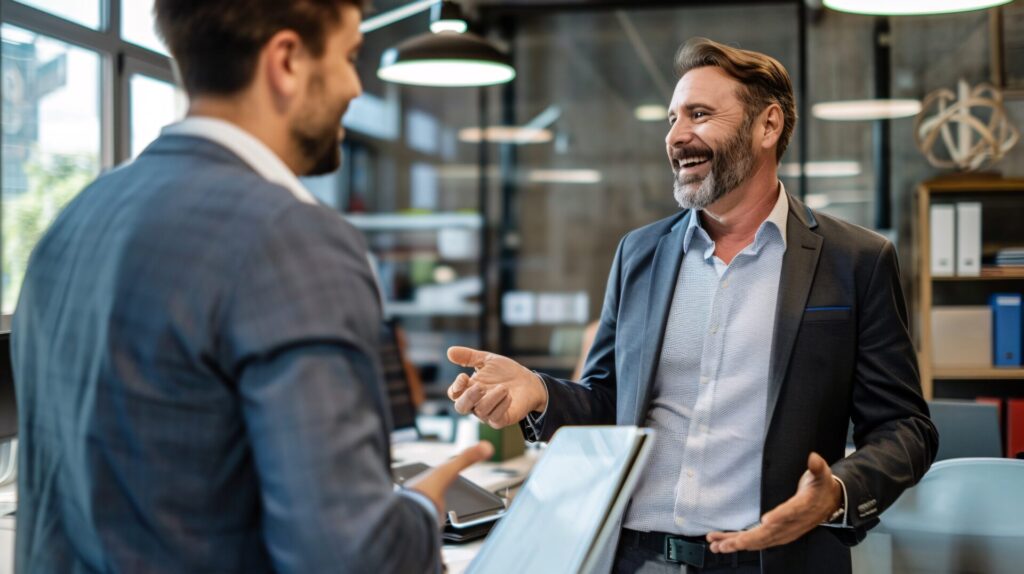
当社では、「認証取得」だけでなく、売上アップ・リスク低減・ブランド強化まで見据えたコンサルティングサービスを提供しています。顧客要求が厳しい自動車や航空機産業で数多くの経験に基づき、現場で負担なく運用できる仕組みづくりを徹底的にサポートいたします。
もし、「うちの現場にも当てはめたいけれど、具体的に何から着手すれば…?」とお悩みでしたら、ぜひ初回30分の無料相談をご利用ください。
当社の詳細については、「会社概要」からご覧いただけます。
さらに学びたい方へ
認証取得の最初の一歩、
「どこから手をつければ…」と
悩んでいませんか?
認証取得に向けた、
具体的な7つのステップを
ご紹介します。
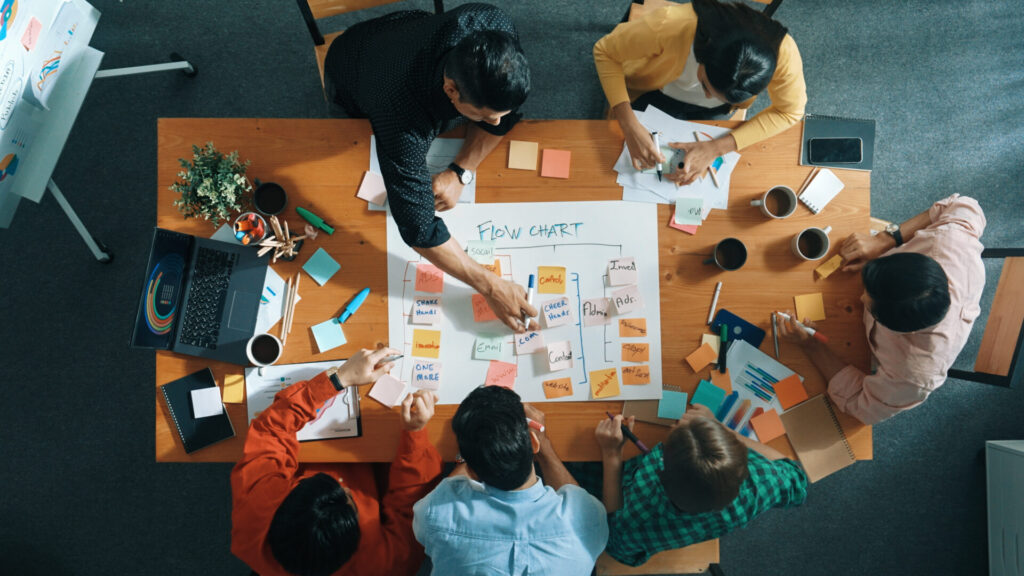
FMEAに関することで
悩んでいませんか?
お客様の現状をお聞きし、
専門家による最適な解決策を
ご提案します。
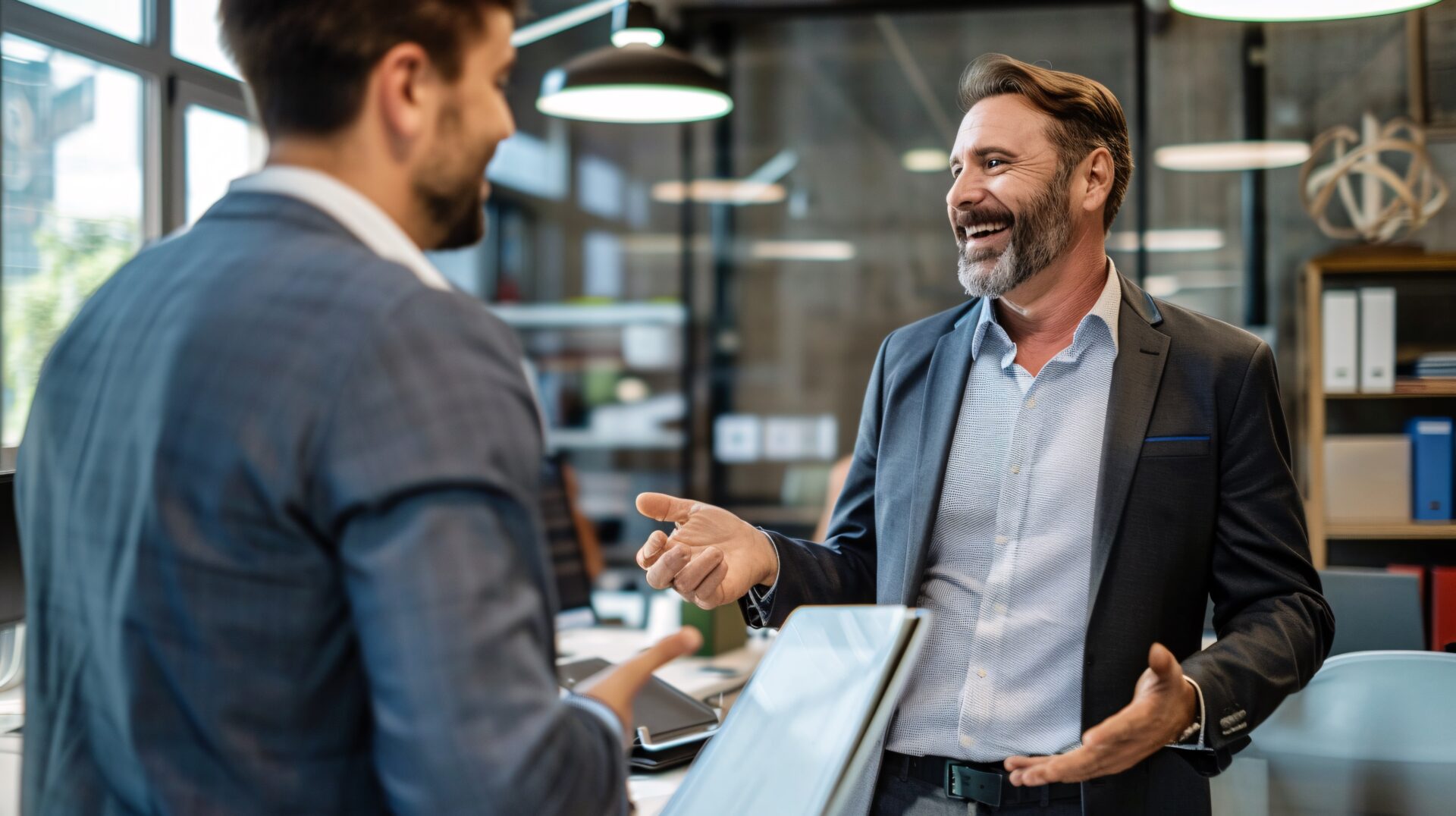
同じ不具合が繰り返される原因、根本的に解消できていますか?
効果的な是正処置の考え方を
詳しく解説しています。
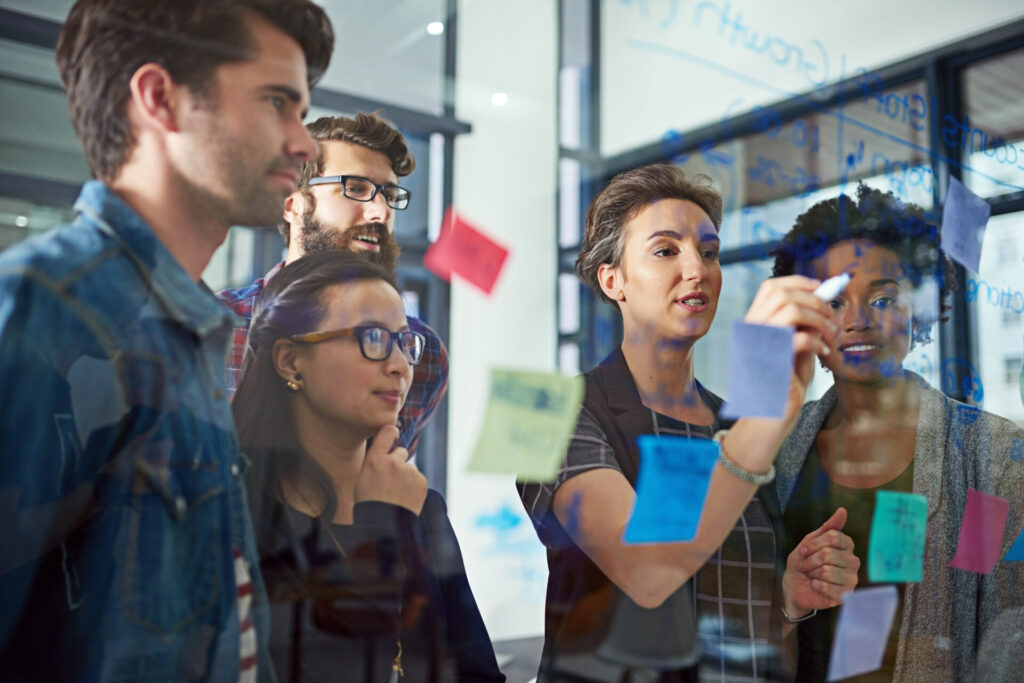
IATF 16949やJIS Q 9100に関する【お役立ち情報】を、他にも多数ご用意しています。
わかりやすい解説や、役立つノウハウを多数掲載していますので、ぜひ以下のページもご覧ください。
お役立ち情報一覧」を見る